Are semiconductor plants too sensitive?
Semiconductors | 08-03-2021 | By Robin Mitchell
Recent extreme weather in Texas has left thousands without power, many being charged extortionate amounts on their electrical bill, and semiconductor plants out of operation. What events have caused production rates to drop, what caused the water shortage, and are semiconductor plants too sensitive?
Winter is Coming – How Snow Made Everything Worse
The COVID pandemic has had a massive effect on all areas of industry with both small and large businesses alike closing down as a result of lockdowns. The reduction of automotive sales as a result of COVID saw a reduction in demand for automotive components, including automotive-grade integrated circuits.
Since automotive ICs were not needed, many foundries that produce them decided to scale back their fabrication. However, semiconductors take months to produce at a foundry, so if demand suddenly increases, the electronics industry has to wait for foundries to start producing devices again.
This is exactly the problem that the automotive industry has recently faced; now that cars are back in demand, the demand for automotive-grade parts has also skyrocketed, but these parts won’t be available for the next year. To try and help with the surge, some foundries such as TSMC have prioritised automotive customers, but even this still faces long delays.
So how does the automotive industry and COVID related to winter? Turns out, when semiconductor foundries were needed most, a snowstorm in Texas resulted in mass power outages to homes, businesses, and you guessed it, semiconductor plants. The resulting power outages caused the production of semiconductor devices to halt mid-production, and some processes don’t like to be disturbed half-way. As such, many devices which were under production have to be scrapped, and this results in an additional delay.
No Power? No Water? Water Shortages Hit Semiconductor Plants
If a lack of power was not bad enough, the resulting snowstorm and freezing temperatures have affected water available to parts of Texas including that of semiconductor plants. While the supply of water is steadily improving, the widespread freezing of water sources, as well as the power outages, has effectively limited water supplies.
Samsung Electronics is one business in particular that has been hit by both power and water shortages in Austin, Texas. According to Samsung Electronics, even if power and water are restored, the damage done by the outages will take a significant (albeit not disclosed), amount of time to restart the foundries and get semiconductor production rates up again.
Are semiconductor plants too vulnerable?
Here at electropages, we have discussed multiple times how defending key infrastructure is critical for the defence and stability of a nation. For example, the banning of hardware from China in the US and UK 5G infrastructure can help to strengthen the network while also ensuring reliability. However, other areas of the industry are often overlooked on their importance, and the semiconductor industry is commonly one whose importance is never fully appreciated.
No one can deny the importance of technology and how having the best technology ensures a countries success in the world. The technology of the past was determined with efficiency in steam engines and how much train track a nation laid, but in modern times, technology is measured in transistor size, the number of transistors on a device, and the level of automation, all of which is powered by the semiconductor.
It can be argued that the failure of the many semiconductor plants in Texas is just as damaging as an attack on infrastructure. Therefore, governments around the world may need to start considering the importance of the microchip, and how foundries that produce such devices should be given better support, better infrastructure, and better defensive mechanisms.
Power and water shortages are rare in developed nations such as the US, but even then a power outage or water shortage should not be able to hamper the production of devices that are critical to a functioning economy. Hospitals, for example, are considered critical infrastructure and as such have backup power generators to ensure equipment can still function.
In the case of the semiconductor industry, foundries could start to consider locations next to power plants that can divert power to the factory when the electrical grid fails. Furthermore, foundries could also see themselves constructing their own locally built gas turbine power plants and water storage systems to ensure that even when services are disrupted, they can continue to operate.
Such supporting infrastructure is expensive, and as previously mentioned such events are rare. But considering how important semiconductors are to everyday life, redundant systems may prove to be beneficiary the next time a major snowstorm, hurricane or cyberattack occurs.
Read More
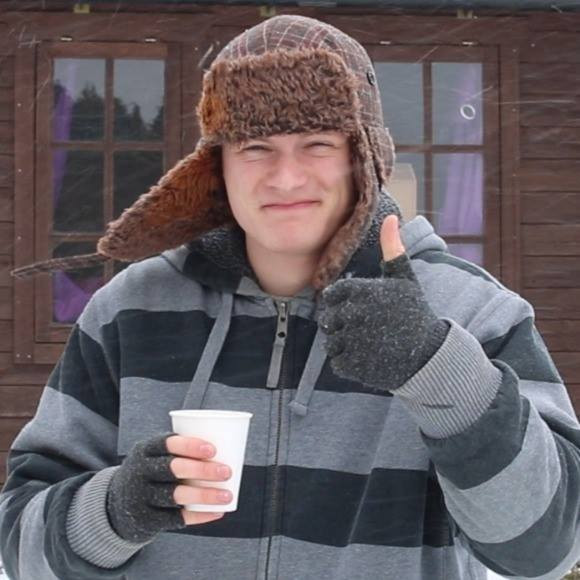