Why the Car Industry is Halting Production
| 18-01-2021 | By Robin Mitchell
Several car makers around the world have begun to halt production due to a shortage of electronic components. What companies have reduced their output, why are they doing this, and what does this teach about supply chains' importance?
Carmakers Reduce their Manufacturing Output
Around the world, carmakers have announced that they are reducing or halting their production facilities altogether. According to various companies, including Volkswagen, Honda, and Ford, the reason is a lack of automotive electronic component supplies.
In response to the shortages, semiconductor manufacturers have said that they will increase their production rates to allow the automotive industry to recover. However, any change in production won’t make any difference until 6 to 9 months due to the length of time taken to manufacture modern semiconductors.
Naturally, cars cannot be manufactured if they lack the parts. Still, there are many manufacturers of electronic components, and how can the supply of automotive parts be critical?
How COVID-19 Cause a Halt in Car Manufacturing
The root cause of the current struggle faced by many cars manufacturers comes from COVID-19; or at least due to global lockdowns and a damaged economy. However, the cause of the component shortage is not as direct as one may think.
The start of the COVID-19 lockdowns saw large numbers of people confined to their homes, and many became unemployed due to the business being unable to function. While many who work in service-based industries continued to operate remotely, the sudden increase in unemployment saw the automotive industry grind to a halt.
However, while car sales reduced dramatically, the sale of consumer electronics increased dramatically due to remote work, which caused a surge in demand for electronic components. Since automotive components were not selling, many semiconductor manufacturers switched their production towards consumer electronics.
Once lockdowns began to lift worldwide, the Automotive market in China and India saw an accelerated recovery, which increased the demand on automotive electronics. However, not having produced automotive grade electronics for almost a year saw the stockpiles of such components quickly diminish, and a worldwide shortage now exists.
Thus, the shortage in automotive electronics resulted from several incidences as opposed to a direct cause. The sudden demand in consumer electronics saw manufacturers switch over, and when the automotive market recovered, key devices which can take up to 9 months to produce had not been produced. Thus, COVID-19 has impacted the automotive market in two waves as opposed to one.
How can supply chains defend themselves?
It is very easy to criticise automotive manufacturers for not stockpiling components or the blame semiconductor manufacturers not sc up fabrication towards the end of the year. In truth, such relationships are extremely complex, and predicting how markets will react is almost impossible.
In the case of automotive manufactures, they could have stockpiled components in anticipation of market recovery, but what would have happened if the market didn't recover? During a time of a pandemic where funds are already running low on keeping employees in furlough, paying for additional components and then storing them could be viewed as a waste of funds. Furthermore, some components have limited shelf-lives (due to oxidation) and may not be usable by the time markets recover.
Semiconductor manufacturers could have continued automotive parts production and even ensured a reasonable amount held in stock in anticipation of market growth. However, just like with automotive manufacturers, those components require storage which carries a cost, and there is no guarantee that the market will recover. Furthermore, the demand for consumer electronics has grown suddenly. Thus it only makes sense for a company during a time of economic difficulties to shift its production into something profitable.
The future of supply chains may take advantage of AI systems that could predict potential shortages and supply chain failures. Such a platform would be linked to multiple companies and market forces that would share data, and the benefit of collaboration is stability. Furthermore, it could improve efficiency in manufacturing stages by better organising how much each product should be manufactured and when.
Read More
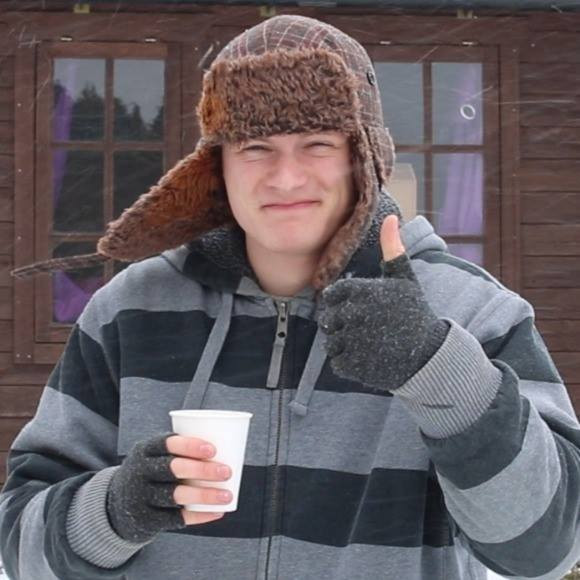