The Future of Soft Robotics: Biodegradable Artificial Muscles & Their Applications
Insights | 27-04-2023 | By Robin Mitchell
Recently, a team of researchers demonstrated a new artificial muscle built wholly from biodegradable components, paving the way for compostable robotic systems. What challenges does soft robotics present, what did the researchers develop, and how could it be helpful for future applications?
What challenges do soft robotics present?
Soft robotics is a rapidly growing field of engineering that involves the design and development of robots made from soft and flexible materials, such as elastomers, hydrogels, and textiles. Unlike traditional robots made from rigid materials, soft robots can perform a wide range of tasks with greater flexibility, dexterity, and adaptability. However, soft robotics also presents a unique set of engineering challenges that must be overcome in order to create reliable, efficient, and practical soft robotic systems.
One of the main challenges of soft robotics is the design of soft actuators, which are the components that allow the robot to move and manipulate its environment. Unlike traditional actuators, such as motors and servos, soft actuators are typically driven by fluid pressure, electroactive polymers, or shape-memory alloys. These materials can be difficult to control and can exhibit nonlinear and time-varying behaviour, making it challenging to model and predict the behaviour of the soft robotic system.
Another challenge of soft robotics is the integration of sensors and feedback systems. Soft robots require precise and reliable feedback to control their movements and interactions with the environment. However, traditional sensors, such as encoders and accelerometers, may not be suitable for soft robots due to their rigid and bulky nature. Soft sensors, such as strain gauges and pressure sensors, must be carefully integrated into the soft robotic structure without compromising its flexibility and compliance.
Soft robots also face challenges in power and energy management. Soft actuators can require high pressures or voltages to operate, which can be difficult to sustain over long periods of time. Additionally, soft robots may need to operate autonomously, requiring efficient power sources that can be integrated into the soft structure. Researchers are exploring new approaches to energy harvesting and storage, such as using conductive textiles or triboelectric generators.
Finally, soft robotics face challenges with the development of suitable materials and manufacturing processes. Soft robots require materials that are both soft and strong, able to withstand repeated deformation and stretching without tearing or breaking. Additionally, soft robots often require complex and intricate shapes that can be challenging to manufacture using traditional methods. Researchers are exploring new materials, such as shape-memory polymers and programmable textiles, and new manufacturing techniques, such as 3D printing and soft lithography, to address these challenges.
Researchers demonstrate biodegradable artificial muscles
Researchers demonstrate biodegradable artificial muscles A team of engineers, led by CU Boulder graduate student Ellen Rumley, has created a new type of robotic actuator, or “artificial muscles,” that can power robotic arms and legs with life-like movements and gradually disintegrate in soil over a few months. This is a significant development in the robotics industry because robots have resulted in technological waste and unsustainable disposal practices. Electronics waste, for example, contributed 53.6 million metric tonnes of unrecycled waste in 2019, which is predicted to rise by over 2 million each year.
The project is a collaboration between researchers from CU Boulder and the Max Planck Institute for Intelligent Systems in Stuttgart, Germany. Ellen Rumley, a graduate student in the Paul M. Rady Department of Mechanical Engineering at CU Boulder, co-authored the study published in the journal Science Advances.
The project has its roots in a long-standing initiative spearheaded by Christoph Keplinger, who was previously an assistant professor of mechanical engineering at CU Boulder and now serves as the director at the Max Planck Institute for Intelligent Systems in Stuttgart, Germany. In 2018, Keplinger and his team introduced a series of artificial muscles known as Hydraulically Amplified Self-Healing ELectrostatic (HASEL) actuators. These actuators, similar to human muscles, enable robotic arms to flex like a bicep and provide grasping capabilities for robotic hands and claws.
The MPI-IS has developed a robotic gripper prototype composed entirely of sustainable materials. (Credit: MPI-IS)
The new actuators are made entirely of sustainable materials and are as versatile as typical Hydraulically Amplified Self-Healing Electrostatic (HASEL) actuators, with the ability to flex for 100,000 cycles or more without breaking. The sustainability of the new materials system opens up exciting options for applications that require components meant for single- or short-term usage, such as food processing or medical applications.
“It was particularly exciting that we ended up with a materials system that is fully biodegradable and can still match key performance metrics of actuators made from non-biodegradable materials,” said Keplinger, co-founder of Artimus Robotics, a Boulder-based company that develops and sells HASEL actuators.
“The sustainability of the new materials system now opens up very interesting avenues for applications that require components designed for single- or short-term use, for example, in the area of food handling or medical applications.”
The decomposition of biodegradable HASEL actuators over a period of 50 days was captured in time-lapse images. (Credit: MPI-IS)
The HASEL actuators are made up of biodegradable transformer oil contained within plastic pouches that are partially covered by a thin coating of an electrical conductor. When electricity is delivered across the HASEL actuators, the pouch “zips together,” squeezing the fluid from one end to the other, altering the shape of the pouch and exerting force on devices such as robotic limbs.
The details of this research can be found in the team's paper published in the journal Science Advances. The researchers tested various biodegradable candidates, including a biodegradable polyester blend, to replace the plastic pouches in their actuators. They demonstrated that their final designs for artificial muscles can lift nearly as well as traditional HASEL actuators and degrade in a composting facility in about six months.
How can such soft robotics help future applications?
The emergence of biodegradable soft robotics is a significant development in the field of engineering, offering new opportunities for sustainable technology and reducing the environmental impact of robotics.
These devices have the potential to revolutionise many industries, particularly those in which robots are used for short-term or disposable applications, such as food processing or medical procedures. Biodegradable soft robotics could replace single-use devices in certain applications, which would reduce waste and lower costs. Additionally, biodegradable soft robotics can be used in applications where rigid, non-biodegradable materials are unsuitable, such as in wearable technology or medical implants.
Biodegradable soft robotics can be used in applications where rigid, non-biodegradable materials are unsuitable or could pose risks, such as in wearable technology or medical implants.
One of the main advantages of biodegradable soft robotics is their ability to conform to irregular and delicate surfaces. This makes them ideal for applications in which the robot must interact with or navigate through complex environments, such as inside the human body. Soft robotics have the potential to be used in various medical procedures, ranging from drug delivery to minimally invasive surgery.
The sustainability of biodegradable soft robotics also has significant implications for the environment. Electronic waste is a growing problem, with millions of tonnes of unrecycled waste produced yearly. By creating devices that can be safely disposed of in composting facilities, we can reduce the environmental impact of robotics and promote a more sustainable future.
Overall, the development of biodegradable soft robotics is an exciting development for the field of engineering. As technology continues to advance, prioritising sustainability and reducing our environmental impact is essential. Biodegradable soft robotics represents a significant step forward in this regard, offering a new generation of devices that are both functional and environmentally friendly.
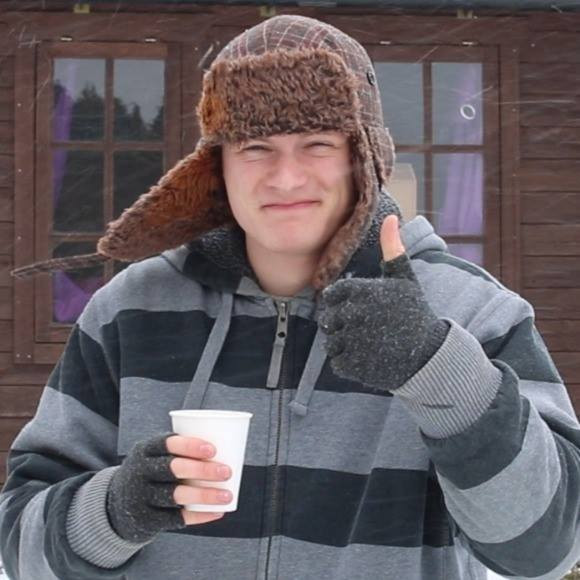