Printing Self-healing Magnetic Field Sensors
Insights | 23-11-2022 | By Liam Critchley
Wearable technologies are gathering a lot of interest in many technological fields, industries and application markets and come in all shapes and sizes (and material composition) depending on the application in question. As many sectors look towards the next generation of technology and advancements over the status quo—especially in areas such as the Internet of Things (IoT) and augmented reality—wearable technologies are going to be crucial.
Wearable technologies in these higher-tech industries (as opposed to medical applications where they are usually touted) are going to be a key component within these systems, as they offer a communication pathway between the user and the other components in the system. Moreover, there is the potential for wearable technologies to be integrated with a range of different sensors to react to their local surroundings efficiently.
Sensing technologies is the area where there is the most potential for wearable technologies, and several methods for realising sensors in wearable technologies are available. Various printing methods are now being used to create flexible sensing modules, but there are still some challenges when printing certain types of wearable and flexible sensors.
Printing Tactile Sensors with Self-Healing Capabilities
Achieving high performance and long-lasting properties in self-healing printable sensors comes down to a number of factors, but one of the most important (from a healing perspective) is the ability to form and reform self-healing percolation networks. This is typically achieved using functional filler materials within larger networks.
Alongside an effective percolation path, some other factors need to be considered from a commercialisation perspective, including the cost, scalability and printability of a given method. When it comes to self-healing properties, several requirements need to be met for them to be effective.
The requirements include the need for the self-healing material to have:
- A complete 100% performance recovery
- The ability to heal repeatedly over multiple cycles
- A fast-healing time
- The ability to operate at room temperature
- For the performance to not be affected by humidity and general ambient conditions
- No manual reassembly for applications where manual touch is not possible (such as in implantable monitoring devices)
Creating printable and self-healing sensors that fit all these requirements have been challenging and often involved some trade-off. However, there have been some tactile printable sensors that have self-healing properties and are stable. As we move towards a post-COVID-19 world, there’s been a lot of information put out there regarding how bacteria and viruses can stay on surfaces for a long time. When looking towards augmented reality applications, there’s a lot of interest in creating touchless interfaces to stop the spread of pathogens while still offering an immersive experience for the user—so many of the physical touch sensors are not going to be suitable for some applications.
Expanding the Scope to Magnetic Field Sensors
There are touchless sensors that can be enabled by optical and electrical capacitive sensors; however, they are quite prone to environmental disturbance. On the other, magnetic field sensors present an opportunity in this area as they are not affected by environmental factors such as humidity and opaque obstacles, so they could offer an alternative option for wearable sensors in augmented reality applications.
While much progress has been made in this field, there are still some challenges around creating printable magnetic field sensors with a high magnetoresistive response with low noise and high resolution—particularly in magnetic field strengths that are suitable and safe for human use. Once combined with the need to self-heal, it has created further challenges because many of the self-healing percolation reforming networks cannot be practically applied to printable magnetoresistive sensors—as many of them involve changing the characteristics of the filler in the composite, which can negatively affect the magnetic performance of the sensor.
Developing Printable and Self-Healing Magnetic Field Sensors
New research has emerged that looks to tackle the filler-to-magnetoresistive property dilemma head-on by using magnetic iron-nickel microparticle filler materials that are driven and guided by alternating magnetic fields (AMF) to form self-healing percolation networks.
The research team created the printable magnetoresistive sensors and found that they had achieved an enhancement in sensitivity on the order of 1 and 2 magnitudes greater than previous reports in this area. Overall, the new sensors demonstrated a low noise and a high resolution and were compatible with a number of printing techniques, substrates and polymeric binder materials.
In line with the characteristics detailed above (the requirements for creating printable and self-healing materials), the sensors demonstrated these six characteristics without any trade-off. In terms of the specifics, the AMF-mediated composites achieved a sensitivity of 35.7 T-1 at 0.086 mT, a figure of merit (FoM) of 4.1 × 105 T-2, a low noise of 19 µΩ/√Hz, and a high resolution of 36 nT. Of these characteristics, it’s the sensitivity and FoM that have been improved by 1 or 2 orders of magnitude. Additionally, the magnetic field used was well below the 40 mT limit imposed by the World Health Organization (WHO), making them suitable for human-driven applications.
In these sensors, the device’s performance was found to be independent of the printing technique used because the AMF played a dominant role in establishing the percolation networks, meaning that the fabrication process is suitable with a range of printing techniques. It was also found that other magnetic filler materials, such as nickel-cobalt and surface-oxidised iron nanoparticles, could be used to create the sensors.
Using the AMF, the healing process of the device is done in seconds at room temperature conditions, regardless of the humidity, and doesn’t need any form of manual reassembly. The magnetoresistive performance also showed no signs of degradation after multiple times of damage and self-healing cycles, promoting long-term stability. The healing process has been attributed to the controllable attraction and oscillation of magnetic fillers in the presence of the AMF that promotes compact arrangement and close contact, leading to percolation network reformation.
The ability to create printable, self-healing and non-touch sensors could also open many doors beyond the human-machine interface in augmented reality applications as well. Some of the ideas being touted include biomonitoring, smart textiles for safety applications, medical therapies, reshapeable soft robotics, and implantable electronics where the electronic components can repair themselves in-vivo without the need for a surgical replacement.
Reference:
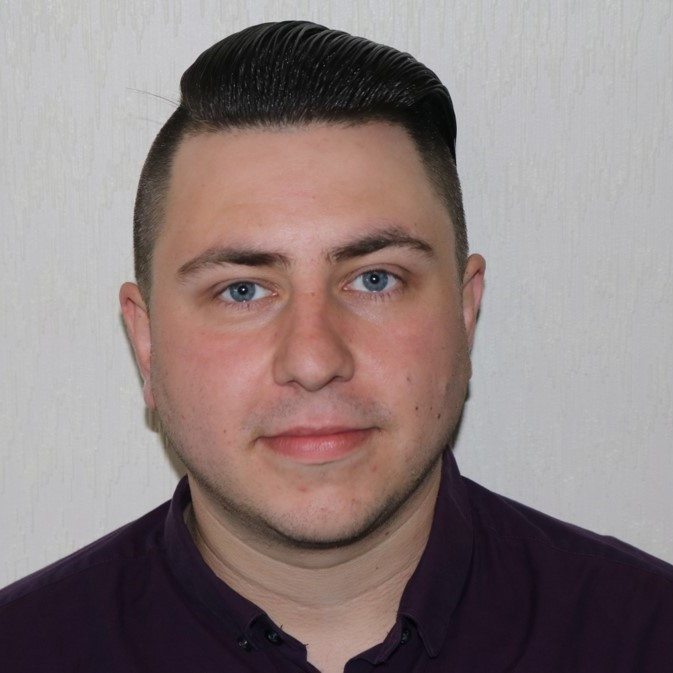