Harvesting Heat from Industry using Thermoelectric Devices
| 16-02-2022 | By Liam Critchley
Many industrial processes are energy-intensive, and many modern industries consume a lot of energy throughout their operations. There are several manufacturing industries where a large amount of energy is lost, making many of these industrial processes very energy inefficient. In many of the manufacturing and process plants in operation today, over 60% of the total energy in the system is dissipated as waste heat energy.
While this energy loss is a massive waste, the high-temperature waste heat can be collected and reused in different industrial processes, saving money and creating a more circular process. However, while the higher heat emitted is easy to harvest (as it tends to be a higher quality form of energy), harvesting the lower temperature waste heat has been more of a challenge. This lower temperature heat is typically seen as a lower quality energy source (because it has a lower energy density) and is emitted at 300°C or less temperatures.
One of the challenges is that the lower grade waste heat accounts for around one half (50%) of all the emitted waste heat. So, manufacturers and process plants can only effectively harvest half of the potential heat energy given out by their processes, and the ability to harvest the full spectrum of heat energy could help further reduce energy usage and costs. Different solutions are emerging to harvest this lower temperature heat energy, and one of the cleaner and more silent solutions suggested in recent years is thermoelectric devices.
Using Thermoelectric Devices to Harvest Heat
Thermoelectric devices are a clean energy conversion technology that can transform waste heat energy into electricity and can be used to reduce fossil fuel consumption by recycling the energy used. These devices directly convert the heat into electricity using the Seebeck effect (a specific form of the thermoelectric effect).
These devices typically use a thermocouple to generate electricity because a voltage is produced across the device when heat is transferred from one side of the device to the other side—generating a temperature difference. This temperature difference generates an applied temperature gradient at the atomic level, forcing the charge carriers within the device to move the hot side to the cold side, generating a current in the process.
The conversion efficiency of a thermoelectric device depends upon many different factors, including the thermal conductivity and electrical conductivity of the devices and the absolute temperature of the heat being harnessed. Because the temperature is a driving factor of the conversion efficiency (deduced by an efficiency equation), it is harder to realise a high efficiency at low temperatures compared to mid-range and high temperatures.
Tellurium-Based Thermoelectrics: The Most Popular Device So Far
As it stands, tellurium-based thermoelectric devices are the only ones capable so far of harnessing low-temperature heat, and high performing devices have been limited to Bi2Te3 alloys only. In today’s market, only n-type and p-type Bi2Te3 alloys are being commercialised for low-temperature heat recovery. Still, more options are being sought because these alloys can only be used in specific scenarios.
While Bi2Te3 alloys are thermodynamically stable at high temperatures, the thermoelectric devices using them are limited to operating temperatures of 177°C (450 K) and lower. This is because a detrimental bipolar effect forms in these semiconductor materials due to the bandgap being very narrow at temperatures above 177°C. Inefficiency terms, this bipolar effect stunts the device’s efficiency and only offers around 7% efficiency for low-temperature heat recovery above 177°C (and 9% below).
Beyond the low performance at the higher end of the low-grade waste heat, the scarcity of tellurium in the world is of concern for the commercialisation of these low-temperature energy harvesters. As it stands, the maximum output power to raw material cost ratio for Bi2Te3 thermoelectric devices is around 17 W/$. The device fabrication itself is also not cheap because the thermoelectric performance of these alloys is limited to along certain crystallographic directions, so the alloy needs to be correctly formed in the device before it is effective. So, new devices are being sought that are cheaper and offer high efficiency across a wider spectrum of the lower temperature harvesting range (less than 300°C, rather than less than 177°C).
Creating Tellurium-Free Thermoelectric Devices for Harvesting Industrial Heat
Creating any type of thermoelectric device typically requires both p-type and n-type semiconductor materials with similar performance levels. Thermoelectric materials composed of magnesium and antimony have recently been shown to be a lower-cost option for replacing Bi2Te3 as the n-type material for temperatures up to 427°C (700K). But two types of semiconducting materials are required, and it has emerged that thermoelectric materials composed of cadmium and antimony could be comparable to Bi2Te3 as the p-type material at harvesting temperatures up to 327°C (600K). A research team has taken these two non-tellurium materials to create a device that can harvest the lower grade, low-temperature heat energy emitted from industrial processes.
The n-type magnesium and p-type cadmium materials were fabricated into a device alongside chemically inert Ni/Fe/Mg3SbBi and Ni/Sb/CdSb metal contacts to prevent chemical diffusion across the device and provide a low interfacial resistivity and improve the overall efficiency of the device. The device achieved a thermoelectric efficiency of 8% at temperatures of 277°C (550 K). While this in itself is still relatively low, it is the highest efficiency outside of tellurium thermoelectric devices—and it is only 1% behind the 9% efficiencies of n-type/p-type tellurium thermoelectric devices at very low temperatures. It is ahead in the higher regions of the low-grade heat range.
Even though the efficiencies are similar, the real difference between this device and the all-tellurium devices is the raw-material cost to the output power ratio because of the much lower raw material cost. All-tellurium devices offer a 17 W/$ ratio; these new non-tellurium devices offer a ratio of 272 W/$, which is 16 times greater than the devices being looked at for commercial applications. Beyond this improvement, these non-tellurium thermoelectric devices can harvest heat up to 327°C and have a stable operating efficiency over a range of 270°C, so they are better over a wider temperature range.
So, even though there is still room for improvement for these thermoelectric devices in terms of their efficiency, these tellurium-free devices are much cheaper to produce, and if tellurium-based can be seen as a commercially viable option, then there is the potential for tellurium-free devices to offer an alternative to the current Bi2Te3 monopoly in the market for low-temperature waste heat recovery.
Reference:
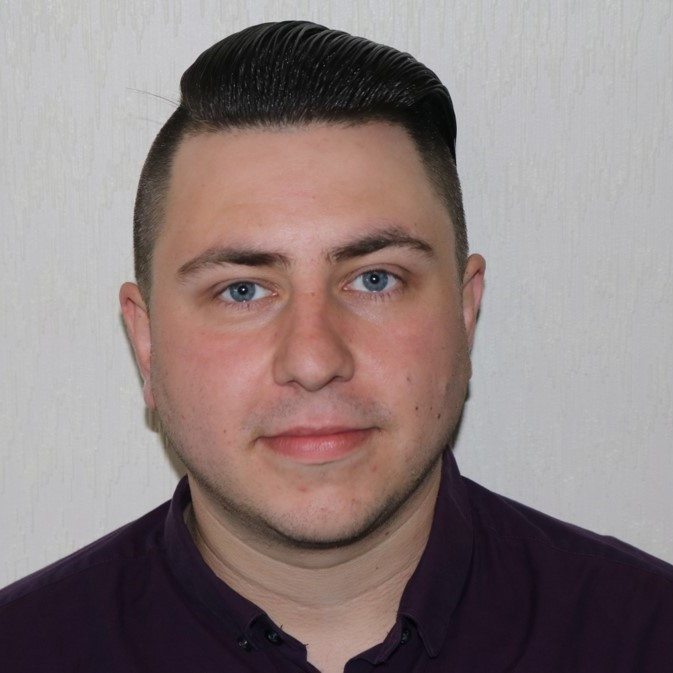