Petasense Vibration Sensor and IIoT 4
| 09-07-2020 | By Robin Mitchell
Last week, Petasense announced their latest vibration sensor, the Vibration Mote 3, with enhanced features for use in IIoT. How it IIoT changing industries, and how does this tie into predictive maintenance?
Introducing IIoT
While internet-enabled devices have been around since the conception of the internet, the ability for even simple devices to have internet access has only been around for the past decade thanks to the ever-increasing transistor count in semiconductors, as well as the reduction in their cost. Now, items that would often not be considered worthy of internet access such as kettles and toasters are being made internet-enabled. While providing such devices with internet capabilities can be considered a novelty as opposed to practicality, the ability to integrate such technologies into even the simplest circuits has opened industrial systems to a whole new paradigm known as the Industrial Internet of Things, or IIoT for short. In IIoT, all aspects to an industrial process are monitored, and data gathered, generally to a central control system or cloud storage system. This allows for industrial processes to be monitored and controlled remotely, which is advantageous for both operators who can be in any location around the world, and managers who may need to track machine uptime. However, data gathering on this scale has also led to industrial systems incorporating AI which can perform predictive tasks. For example, sensory information from a piece of equipment can be used by an AI system to determine if the equipment is close to failure. From there, appropriate measures can be taken before any permanent damage is done, thus avoiding machine downtime.
Petasense Vibration Mote 3
When developing IIoT systems, it is important that the sensors used are not only reliable, but must also have the resolution that allows for detecting abnormalities. Last week, Petasense announced their latest vibration sensor, the Vibration Mote 3, which addresses major challenges in Industry 4.0 adoption. The Vibrate Mote 3 (VM3), is capable of measuring vibration, speed, and temperature for use in continuous monitoring of variable speed assets. While AI is useful for predictive monitoring, it is not so great in scenarios which involve intermittent operation or variable speeds as these are environments where the equipment is not subjected to a stable operating environment. The VM3 helps with this by offering event-based measurements which include readings when a specific speed is met, and the result is consistent readings with up to 5 years of operation on a single battery.
Credit: Petasense
The VM3 also offers additional features to improve performance and reliability in industrial environments, including data backup during network downtime, data transmission over Wi-Fi, and the ability to be remotely monitored via a network connection. The Petasense VM3 is a 32-bit ARM Cortex M4F clocked at 144MHz, and is powered by a CR123A 3V Lithium battery. The vibration sensor is a triaxial MEMS device with a frequency response of 2 to 5,500 Hz (+/- 3 dB), measurement range of +/- 2g to +/- 16g, a resolution of 16-bits, and sampling rate of 26.7 kHz. The temperature sensor has a measurement range of -40°C to 85°C, while the magnetic sensor has a measurement range of Full scale adjustable from +/- 4 gauss to +/- 16 gauss.
"VM3 is truly a step change in wireless sensors. The smart measurement features are unique in the industry. We leverage edge computing to collect sensor readings at the perfect time, taking synchronous measurements and more comprehensive readings based on the condition of the prior reading. It allows you to monitor speed and operating state, taking readings only when assets are running."
-
Kuldeep Amarnath, CTO at Petasense
Conclusion
While not a component itself, the Petasense VM3 demonstrates the importance of IoT technologies in industrial processes, and the ability to run a device for 5 years on a single battery can be highly advantageous. The ability to gather large amounts of data behind industrial systems allows for predictive maintenance, as well as the possibility of improving those systems with better time management and waste reduction.
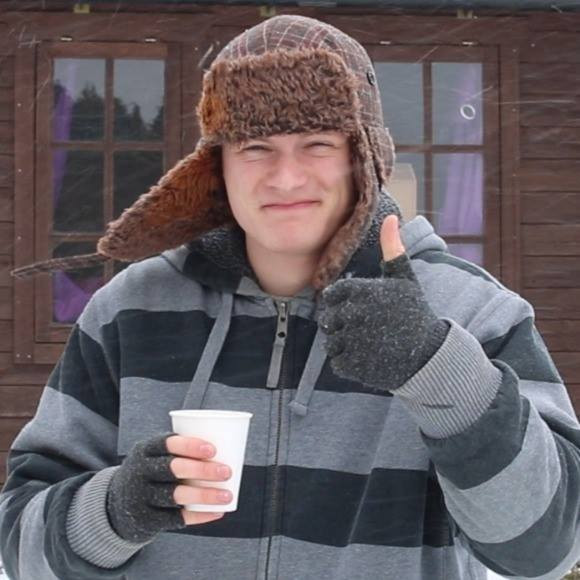