MIT Engineers 3D Print Electromagnets: Redefining Components
Insights | 19-03-2024 | By Robin Mitchell
The researchers adapted a multimaterial 3D printer to enable the one-step printing of compact solenoids with magnetic cores. This approach removes the potential for defects typically introduced in post-assembly stages.
Key things to know:
- MIT's Innovation in 3D Printing: Researchers at MIT have developed a fully 3D-printed solenoid that showcases the potential to significantly alter electronics manufacturing, capable of generating a practical magnetic field.
- Advantages of 3D Printing in Electronics: 3D printing, particularly Fused Deposition Modelling (FDM), offers unparalleled flexibility in component design, allowing for complex 3D geometries and the integration of circuits into product enclosures, potentially reducing costs and waste.
- Breakthrough Solenoid Design: The MIT team's solenoid is more compact, efficient, and powerful than existing models, demonstrating the feasibility of 3D printing for producing advanced electronic components.
- Future Implications: The advancements in 3D-printed electronics could have significant implications for sustainable manufacturing, low-cost medical systems, and even long-term space missions, highlighting the technology's versatility and potential for global impact.
Pushing the boundaries of 3D printing, researchers from MIT have recently demonstrated a fully 3D printed solenoid capable of generating a practical magnetic field. What makes 3D printing potentially massive in the field of printed electronics, what did the researchers demonstrate, and how could 3D printing become the future of electronics?
What makes 3D printing potentially massive?
Since the development of the first electronic components, numerous manufacturing technologies have emerged that allow for all kinds of technology to be realised. Laser cutting has allowed for resistors to be trimmed to precise resistances, physical vapour deposition has allowed for ultra-thin layers to be formed on top of semiconductors, and high-speed precision stepper motors and servos allow for pick-and-place machines to operate at unbelievable speeds when populating PCBs.
Despite the crucial role of various manufacturing processes in the development of numerous technologies, no single technology offers a comprehensive solution. Each relies on additional industrial processes and manufacturing steps to complete a component, circuit board, or product. This complexity is not typically a concern for mass-produced items but poses significant challenges for prototype production due to high tooling costs and production intricacies.
Advancing Electronics with 3D Printing Technology
In contrast, 3D printing has seen remarkable growth over the past decade, particularly in the electronics sector, where it holds the potential to replace many traditional electronic component manufacturing technologies. Among the various 3D printing methods, Fused Deposition Modelling (FDM) stands out for its promise in creating printed components.
Simply put, FDM printers build models layer by layer, usually using an extruder to deposit some material at a high temperature so it fuses with layers below it. If multiple nozzles and feedstock are used, it becomes possible for an FDM printer to print different materials as needed, and due to the ability to print in 3 dimensions, any material can be located anywhere in a design.
The most common use of multiple material printing is coloured filament, so that printed models are coloured, requiring no additional processing. However, it is highly anticipated that this same concept could also be used to create electronic components, allowing for circuits to not only be fully customisable, but be built in all three dimensions.
This means that components could be made out of complex 3D geometries, taking full advantage of the z-height as well as the x and y planes. Not only does this allow for significantly denser circuit designs, but the use of FDM printing technology could help to reduce the cost of producing individual prototypes, as there is no need for any tooling.
Furthermore, this design concept also allows for circuits to be embedded into the enclosure of a product, thereby making the most of the structural components of a product. For example, enclosures could have antennas, analogue circuits, sensors, and much more printed directly inside the wall cavities, reducing PCB space and eliminating the need for additional manufacturing processes.
MIT researchers create 3D-printed solenoid
Recognising the advantages in 3D printing technologies, MIT has been actively researching the field to try and find real-world uses, such as low-cost medical systems. Now, MIT has demonstrated a 3D printed solenoid that is capable of producing a magnetic field.
The breakthrough by MIT researchers in creating a fully 3D-printed solenoid that can generate a practical magnetic field is a testament to the innovative strides being made in the field of electronics. By modifying a multimaterial 3D printer, the team was able to print compact, magnetic-cored solenoids in one step, eliminating defects that might be introduced during post-assembly processes. This customisation allowed the solenoids to withstand twice as much electric current and generate a magnetic field three times larger than other 3D-printed devices. Such advancements could significantly lower the cost and increase the efficiency of producing electronic components, showcasing the potential of 3D printing to revolutionise electronics manufacturing.
According to the researchers, the solenoid is able to withstand up to 2 times the input current and produce 3 times the magnetic field compared to other solenoids printed by other researcher. Furthermore, the solenoid itself is estimated to be around 33% smaller than others currently in development, demonstrating a significant improvement in 3D printed electronics.
To illustrate the innovative design of the 3D-printed solenoid, Figure 1 provides a detailed view of the solenoid's structure, showcasing the three-dimensional rendering and exploded view. This visualisation highlights the intricate arrangement of conductive spirals and insulation layers, pivotal in achieving the solenoid's enhanced magnetic field generation capabilities.
Figure 1: Depiction of a 3D-Printed Layered Solenoid: (a) a three-dimensional illustration and (b) a detailed breakdown, illustrating the alternating layers of conductive spirals and insulating materials.
To achieve this design, the researchers turned to a precision FDM printer capable of working with multiple materials. Additionally, the researchers modified the printing head so that it could work with pellets instead of filament, as pellets are far easier to obtain. In the case of the magnetic nylon material used to create the core, producing filament is virtually impossible, so having the ability to print from pellets reduces design complexity while giving the printer more access to materials.
Figure 7 showcases a three-dimensional, monolithically 3D-printed FeSiAl Nylon-cored eight-layered solenoid, juxtaposed next to a US quarter for scale. This figure exemplifies the compact size and the precision achievable with the modified 3D printing technique, underscoring the potential for miniaturisation in electronic components.
Figure 7: A Three-Dimensional, Single-Piece 3D-Printed Solenoid with a FeSiAl Nylon Core, Spanning Eight Layers: (a) displays a top view alongside a US quarter for scale comparison, and (b) presents a sectional view placed over a US quarter.
Each layer of the solenoid was printed with a spiral conductor, a magnetic core, and an insulating layer to keep layers separated from each other. When combined, the spirals allow for electromagnetic properties, thus realising the solenoid.
How could 3D printing become the future of electronics?
Undoubtedly, 3D printers present a massive opportunity in the field of prototypes and low-volume production due to their ability to build anything without requiring any tooling. However, this also means that they are less suitable for mass production due to their slow manufacturing speed and generally worse quality compared to dedicated discrete components.
However, one area that could see major benefits is long-term space missions. In the case of future missions to other planets (such as Mars), the limited space on crafts, the long duration of the mission, and the inability to get new parts mean that stocking spare modules and electronics will be challenging.
Demonstrating the practical implications of these advancements, Figure 10 compares the magnetic field strength at 0.5mm from the coil top versus current for solenoids with different core materials, including the FeSiAl Nylon-cored solenoid developed in this work. This comparison highlights the significant improvements in magnetic field generation, pivotal for the development of more efficient and compact electronic devices.
Figure 10: Comparison of Magnetic Field Strength 0.5 mm Above the Coil Top Against Current for Fully 3D-Printed Solenoids: Featuring air-core with ten layers (indicated by black markers, PowerMEMS 2022) [Citation40], iron PLA-core with eight layers (shown with green markers, CPEEE 2023) [Citation41], and FeSiAl Nylon-core with eight layers (represented by pink markers, from this study).
Instead, if such devices could be printed as needed, then only the raw materials would be needed. As these raw materials can be used for numerous designs, it becomes possible to print what is needed as it is needed. Thus, a mission that never required a new communications board but needed ten replacements for an engine controller could easily achieve this with just the raw materials and a printer.
3D printing could also be the key to low-cost electronics in economically deprived nations where access to new equipment is challenging. While the printer itself would be expensive, its ability to print anything gives an immense amount of freedom, including the ability to print medical sensors, equipment, and other life-saving devices.
Conclusion
Overall, what the researchers have demonstrated with their 3D printed solenoid is impressive, and clearly shows that 3D printed electronics are not just possible, but perfectly plausible.
The implications of MIT's 3D-printed solenoids extend beyond just the creation of more efficient electronic components. The ability to produce these solenoids on-demand, with reduced material waste and without the need for complex assembly lines, presents a compelling case for the role of 3D printing in achieving sustainable and cost-effective electronics manufacturing. Furthermore, the adaptability of 3D printing technology to utilise a variety of materials opens up new possibilities for customising electronic components to specific needs, potentially leading to innovations in medical devices, consumer electronics, and even space exploration technologies. As 3D printing continues to evolve, it could indeed become a cornerstone of future electronics, offering solutions that are not only technologically advanced but also environmentally responsible and accessible to a broader range of creators and innovators.
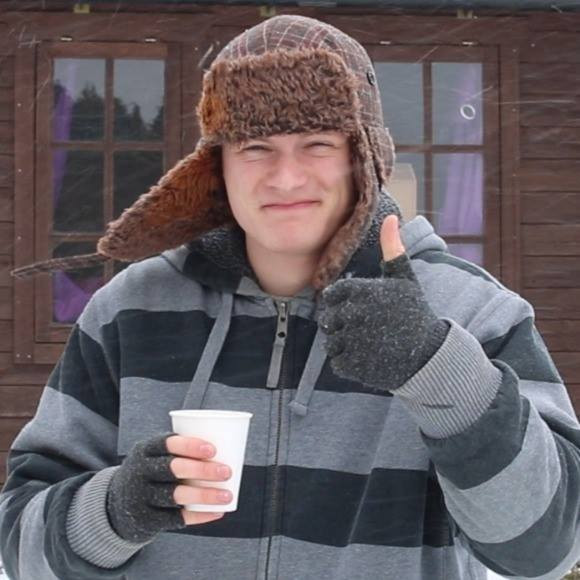