Advancing Piezoelectrics: 3D Printing and Miniaturization
Technical Analysis | 31-05-2023 | By Liam Critchley
In the ever-evolving landscape of electronic engineering, piezoelectric materials stand out as a cornerstone for a myriad of electronic devices. Harnessing the piezoelectric effect, these materials ingeniously convert mechanical movement into electricity and, intriguingly, can also reverse the process. This dual capability positions piezoelectric materials as vital components in sensors, actuators, energy harvesters, and ultrasound imaging devices. While these materials have been integral to device development for years, recent advancements in 3D printing and microscale structural design are poised to dramatically enhance the properties, functionality, and anisotropy of piezoelectric devices, marking a new era in their application and efficiency.
Introduction to Piezoelectric Materials and Devices
Piezoelectric materials are used to create different electronic devices. Piezoelectric devices use the piezoelectric effect to convert mechanical movement into electricity but can also work in reverse, and a piezoelectrical material can create mechanical energy in the presence of an electric field. The ability to turn mechanical motion into electrical energy, and vice versa, has meant that piezoelectric materials are widely used materials in sensors, actuators, energy harvesters, and ultrasound imaging devices.
Piezoelectric materials have been used for many years in these devices, but advancements in new structural designs and computational approaches have led to the conclusion that the incorporation of 3D microscale features could help to improve the properties, functionality, and anisotropy of piezoelectric devices.
"Recently, the emergence of new structural designs and computations has led to the prediction that incorporating 3D microfeatures into piezoelectric materials could provide unprecedented properties or functionalities, including designed anisotropy and the ability to emit tailored and localized ultrasound fields, as well as sensors and actuators for miniaturized robots and transducers."[1]
Challenges in Creating Small-Scale Piezoelectric Architectures
However, the realisation of these small-scale architectures is typically dependent on a limited number of machining methods, such as etching, because piezoelectric ceramics materials are brittle in nature (limiting the techniques available). However, they can also be created out of 3D printed composite materials that utilise piezoelectric nanoparticles and polymer matrices (because small-scale materials are needed to craft the small architectures).
But there’s a catch with some of the existing methods. The mechanical stresses caused by machining processes can degrade the piezoelectricity in the finished device, and therefore the small-scale features have much lower piezoelectric coefficients than they should have compared to their pristine counterpart. This also results in lower emissions in devices such as ultrasonic transducers.
The Role of 3D Printing in Piezoelectric Device Fabrication
This is where 3D printing can come in, as it enables small and complex structures to be created much easier than some conventional manufacturing methods. One area where there is interest for using 3D printing is to create small features in piezoelectric devices in ultrasonic transducers. 3D printing can offer a way to fabricate precise microscale features that have a high piezoelectric response and are capable of acoustic focusing. There’s also the potential to create localised energy outputs and tailored and localised ultrasonic emissions that could be utilised in the future in a range of medically focused applications—such as in-situ imaging, cavitation-based drug delivery and neuromodulation therapy areas.
The performance of ultrasonic transducers is closely linked to the piezoelectric properties and geometries of the active elements in the device. This is another area where 3D printing is favoured for creating small-scale active features because existing tools for creating piezoelectric elements can only create simple geometries—such as flat disks, cylinders, and cubes—whereas additive manufacturing methods can create all manner of geometries because they are not manipulating bulk materials that are brittle. Instead, 3D printing builds the material up into the desired geometry, and this approach has recently been used by researchers to create ultrasonic transducers with microscale piezoelectric active elements.
In their study, the researchers fabricated a miniaturised ultrasound transducer with curved PZT elements. This was achieved through a novel 3D printing system specifically designed for liquid phase sintering of piezoelectric composites.[1]
"The manufacturing of these architectures is either dependent on conventional machining methods, including etching, dicing and hot pressing due to the brittle nature of piezoelectric ceramic, or limited to 3D printed composite materials containing piezoelectric nanoparticles and polymer matrices." [1]
According to the researchers, '3D printing offers a unique opportunity to fabricate precise microscale features with a high piezoelectric response, opening up new possibilities for the development of ultrasonic transducers.
Additive Manufacturing Techniques for Piezoelectric Ceramics
Advancements in additive manufacturing have enabled much higher freedom when fabricating piezoceramic materials. However, many additive manufacturing methods create devices that have a high porosity and weak piezoelectric response, limiting their use. Many additive technologies do not offer geometric freedom with ceramic materials either, limiting the choices, but there are options.
One approach that is plausible is two-photon lithography with post-process sintering, but the best option is to use light-based stereolithography (SLA) to print piezoelectric parts. This is because piezoelectric nanoparticles can be mixed with photosensitive monomers to form composite colloidal materials. These colloidal materials can then be printed and cured using UV to print parts.
In a lot of studies performed to date, the viscosity of the colloidal printing suspension has made printing uniform layers difficult, broadening the printed features in each part and making printing precise features a challenge. Studies that have created dense parts have been sintered at high temperatures to grow the ceramic grains, but the high temperatures evaporate some of the elements (such as lead) out of the ceramic, which not only suppresses piezoelectric performance but also increases the chance of deformation, crack initiation, and porosity in the printed elements. While SLA-based 3D printing has a lot of potentials, these challenges need ironing out for it to be a feasible technology, and that’s what a recent study has set out to do.
Using SLA to Print Piezoelectric Transducers
Researchers have now adopted an SLA-based additive manufacturing approach, and they optimised a post-processing sintering process so that dense lead zirconate titanate (PZT) elements could be created for improving the piezoelectric response in ultrasonic transducers.
The researchers first trialled a micro-stereolithography method with a tapecasting process to get good control of the green part. Inspired by the liquid phase sintering additives used in this approach—which promotes grain growth and improves the sintering behaviour of ceramics—a liquid phase sintering method was created that is compatible with printing PZT materials using SLA methods. Moreover, the researchers used a liquid sealing method to prevent evaporation of the lead atoms from the ceramic at high temperatures.
Part of their methodology involved a debonding process to burn off the supportive polymer. Additionally, they implemented a liquid sealing process to reduce the lead loss during high-temperature sintering.[1]
The prevention of elemental evaporation led to the printing of piezoelectric elements with a lower porosity and higher performance. The fabricated PZT elements possess a piezoelectric charge constant and an electromechanical coupling factor of up to 583 pC/N—which is 92.5% of the value of the pristine material, showing that there was very little piezoelectric loss in this approach. The values were also higher than piezoelectric elements that have been produced by other printing methods.
a) The schematic illustrates a miniaturised ultrasound transducer equipped with curved PZT elements. b) It also presents the components of the liquid sintering resin. c) A unique 3D printing system is employed for liquid phase sintering of piezoelectric composites. d) The supportive polymer is eliminated through a debonding process. e) The liquid phase sintering (LPS) process is utilised to form a dense PZT sample. f) To minimise lead loss during high-temperature sintering, a liquid sealing process is implemented. g) The 3D printed miniaturised ultrasound transducers, operating at 9.75 MHz, generate acoustic pressure curves that surpass many medical thresholds.
The researchers found that the 3D-printed miniaturised ultrasound transducers, operating at 9.75 MHz, generated acoustic pressure curves that surpassed many medical thresholds. This finding underscores the potential of these devices in medical applications.[1]
As well as the active piezoelectric element, the researchers created printable packaging material pallets composed of a backing layer and impedance matching layer, as well as physical housing material, that tailor the impedances and attenuations coefficients over wide ranges so that the transducers were tailored to different applications.
The researchers fully printed a miniaturized ultrasound transducer using both the microscale active elements and the packaging material. The created device was created to target medical applications and was able to produce a high and localised acoustic pressure in small blood vessels to allow localised cavitation generation, drug delivery and ultrasonic modulation of cellular activity.
According to the research paper, 'the ability to 3D print both the microscale features while retaining a high level of piezoelectricity in the ceramic materials could open new application doors for 3D printed transducers.'[1] This suggests that the ability to create these ultrasonic transducers with high performance and acoustic focusing and cavitation generation within millimetre-sized channels could help to create a range of miniaturised devices that are suitable for different biomedical applications.
References
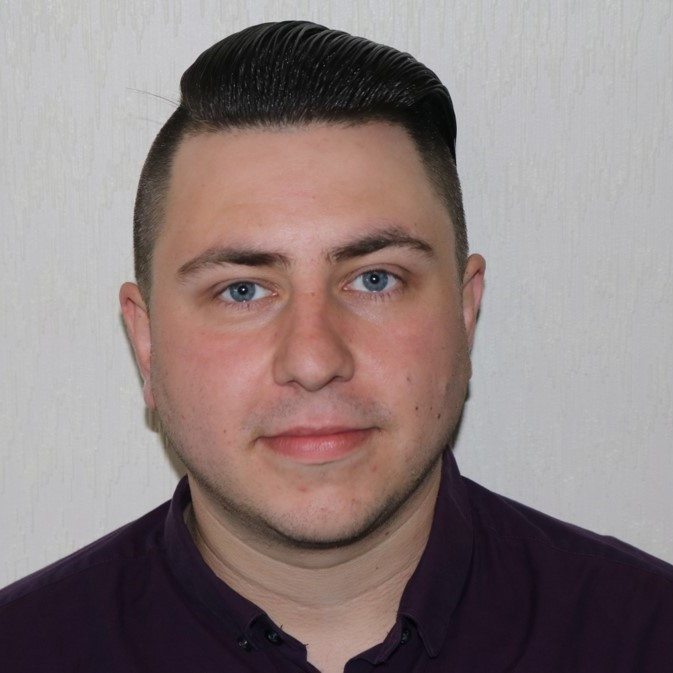