New Bionic Finger Breakthrough: Detecting Substructures in Materials
In The News | 13-03-2023 | By Robin Mitchell
Recently, researchers demonstrated a new bionic finger with subsurface tactile tomography capabilities, enabling it to detect substructures in soft materials and improving the tactile feedback system of robotics. The finger creates a series of slice images of the material, allowing for the detection of subsurface structures with nerve-like sensors, enhancing the handling and balance of robotic systems. While a robot cannot currently hold an egg with the same dexterity as a human hand, this development brings robots closer to achieving human-like detection and manipulation abilities. What challenges do robotic touch systems face, what have the researchers demonstrated, and how could such bionic fingers be used?
What challenges do robotic touch systems face?
There is no doubt that robotics has come a long way since the first robotic platforms found their way into industrial environments. Modern robotic arms commonly found in production plants are capable of lifting immense loads, welding the smallest features, and repeating complex actions with great precision. At the same time, companies such as Boston Dynamics have demonstrated bipedal robots performing backflips while throwing bags of tools up in the air.
And yet, with all of these advances, robotics still face some major challenges. One of these challenges is dexterity, and no matter how well a robotic system is programmed, no robot currently in development has the level of dexterity that the human hand has. The best test case for this is picking up delectate objects such as eggs. It is difficult for a robot to know how much pressure is being exerted on the egg, whereas a human can happily juggle and carry multiple eggs in one hand without breaking any.
The reason why dexterity is such an issue for modern robotics comes down to the sheer computational complexity of dexterity and the need for high-density sensor networks. For example, each fingertip of a human hand has more than 3,000 nerve endings, and these nerve endings are capable of detecting more than just absolute contact; they can detect varying levels of pressure. This high density of pressure sensors enables the brain to recognise not only when contact has been made with a surface but its texture and even structures under the surface. In fact, the human finger is so sensitive it is possible to detect wrinkles on a surface that measure in the nanometers.
Trying to create an electrical equivalent of a human finger would require thousands of sensors, thousands of connections, and high-speed processors. Considering that such technology doesn’t currently exist, robotic systems are still decades away from competing with human hands.
Researchers create bionic finger with sub-surface detection capabilities
Recently, researchers from Wuyi University published a paper on a new bionic finger that can provide improved dexterity to robotics. To create the tactile sensing system, the researchers took a metal cylinder which was mounted onto a finger which serves as the contact point (i.e., the fingertip), while carbon fibre beams are used as mechanoreceptors that are capable of detecting pressure. The finger is then poked into a target of interest, and the resulting force exerted on the finger is recorded. From there, the finger continues to poke different areas of the target, effectively creating a scan of the target. The resulting recorded pressure is then stored in memory, which allows a visual representation of the recorded pressures to be displayed.
The researchers were able to use the device to not only detect the mechanical resistance of materials (indicating if it is soft or hard) but could even detect subsurface structures. For example, the researchers placed the letter ‘A’ made from a hard plastic under a piece of silicone, and the minute pressure changes allowed the device to see the letter despite not making physical contact. In another demonstration, the researchers simulated human tissue by creating a three-layered structure representing bone, muscle, and skin, and the finger was able to distinguish the different layers by only prodding the outer layer of skin.
The bionic finger has been developed with subsurface tactile tomography capability, allowing for the recognition of both surface and subsurface characteristics and the generation of layer-by-layer slice images and 3D profiles of materials, including human tissue and flexible electronics.
How could such bionic fingers be used?
If the design can be miniaturised to provide tens of sensors on a single robotic finger, it is possible to provide existing robotic systems with a great degree of dexterity. The ability to detect the softness of a part can allow robotic systems to pick up objects with the exact force needed, thereby enabling them to be used in more delicate applications.
At the same time, the ability to detect subsurface structures under tissue makes it possible for future robots to perform non-invasive medical examinations, such as searching for potentially cancerous lumps and determining complications with internal organs. It is also possible for a robotic system to perform a blood test using the sensors to identify where blood vessels are.
What the researchers have demonstrated is truly exciting, as robotics has often struggled with dexterity and sensory capabilities. If this technology can be miniaturised, there is no telling what it could lead to.
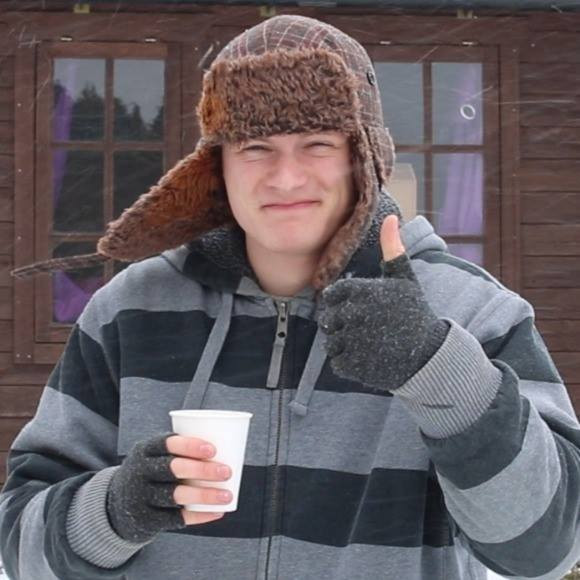