The Importance of EMC in Electronics Product Design & Compliance
24-09-2020 | By Robin Mitchell
When designing electronic products, it is crucial for engineers to consider electromagnetic compatibility (EMC) as it is a vital aspect to ensure the proper functioning and safety of electronic devices and systems. Additionally, product regulations often mandate strict EMC conformity to prevent interference with other devices or systems. Understanding the importance of EMC, how it can be achieved and how to reduce it is vital for electronic product design.
What is EMC?
Electromagnetic compatibility is a crucial aspect of electronic product design that ensures different electrical systems can coexist in the same environment without interfering with each other. In simpler terms, EMC is achieved when a circuit emits electromagnetic radiation (EM) within legal limits and remains unaffected by specified levels of EM radiation. Understanding EMC's importance is vital to successful electronic product design.
Why is EMC important?
The main goal of EMC is to ensure that electronic circuits operate correctly when exposed to external EM radiation and to ensure that the electronic circuit in question does not emit “stray” EM radiation. To better understand why this is important. Let’s take a look at a very famous example of where EMC was not considered; mobile signals. If a phone is placed sufficiently close to a speaker, you can sometimes hear the famous “Bip Bip Bip”. This happens because signals sent by the mobile to the cell tower, despite being well above audio levels, modulate signals at audio frequencies, and the speaker can detect and amplify these signals. In this example, the speaker is susceptible to stray EM radiation from the mobile, and the mobile has generated EM radiation that can affect the performance of other circuits.
Thus, EMC is important in circuit design to ensure that external signals cannot upset the normal operation of circuits and the operation of that circuit does not affect other circuits. This need to reduce interference is the reason why most markets around the world have regulations on how much radiation a circuit can emit and how much interference it needs to be able to handle. Therefore, EMC is also essential to consider, as products cannot be sold if proper EMC controls are not implemented.
The importance of EMC compliance for electronic product design
Electromagnetic compatibility is a critical consideration for electronic product design, particularly regarding compliance with product regulations. EMC regulations are put in place to ensure that electronic products do not interfere with other devices or systems and that they can function correctly in their electromagnetic environment. These regulations are essential to prevent interference and ensure the safe and reliable operation of electronic products in various settings, including homes, workplaces, and public spaces.
Compliance with EMC regulations is also essential for manufacturers and engineers, as non-compliance can result in penalties, fines and even legal action. In addition, if a product is found to be non-compliant, it may be withdrawn from the market, leading to significant financial losses for the manufacturer.
Furthermore, compliance with EMC regulations is also important for the safety of the end users. Products that do not comply with EMC regulations may risk human health and safety and lead to accidents or malfunctions.
Compliance with product regulations is essential for manufacturers and engineers to ensure the safety and reliability of electronic products and avoid penalties and legal action.
How can EMC radiation be reduced?
Improving EMC in a circuit is no small feat, and the nature of EM radiation must be fully understood before trying to reduce it. Generally, there are two methods in which EM radiation can interfere with a device; radiated and conducted. Radiated emissions are those caused by electromagnetic waves (i.e. radio), while conducted are those caused by electrical signals coupling from interfering sources (such as mains hum into a speaker). Methods for protecting against outside interference are also just as effective for protecting outside devices from generated EM interference.
While immunity to EMC is important, it is often best to start with emissions, as this is generally the primary cause for devices failing during the product testing stage. Once emissions are identified, they can be removed by either changing the design to emit less or incorporating methods for absorbing emissions before they get to the outside world.
Reducing Emitted Emissions at the Source
Most emissions from modern electronics come in the form of radio waves, and these are almost always caused by high-speed switching circuitry. Common culprits include switch-mode power supplies (SMPS), motor controllers, radio circuits, high-speed buses, and I/O connectors.
The reason why high-speed circuitry often causes issues is the use of high-frequency square waves with large slew rates (i.e. the sudden change from a 0 to a 1). Square waves can be mathematically modelled as an infinite number of sine waves at odd harmonics combined, and this is exactly what is produced in the EM world. When a signal switches from a 1 to a 0, many radio emissions at odd harmonic frequencies are produced, and these can cause interference in other devices that pick them up. Therefore, such emissions can be reduced by decreasing the slew rate (i.e. making square waves more trapezoid in shape).
In many cases, emissions can come from switching noise (such as those found in SMPS). In these cases, additional components can be added to a circuit to bypass these signals and prevent them from injecting noise into other areas as well as causing emissions. For example, decoupling capacitors placed around integrated circuits not only help to prevent switching noise from interfering with normal operation but can prevent emissions from the power lines. Resistors, capacitors, and inductors can also be used as filter components for I/O and prevent emissions from leaking from I/O connectors and from escaping at I/O cables.
Another method for preventing emissions comes from ensuring that the length of PCB traces are not a multiple of the wavelength of the signal frequency in that trace. Alternating current in a wire produces radio waves whose frequency match the frequency of the AC; this is what an antenna does. But for an antenna to reach peak efficiency, it must be designed so that the length of the antenna is a multiple of the wavelength of the desired frequency. Since an antenna is nothing more than a length of wire, a PCB trace can very easily become an antenna. It’s best to see an example to understand how this works.
A PCB trace is to carry a 2GHz signal, and this 2GHz signal can produce a 2GHz radio signal with an approximate wavelength of 15cm. Therefore, the length of the PCB trace should be less than 15cm and not be a length that is a multiple (i.e. 7.5cm, 1.5cm, etc.).
Absorbing Emitted Emissions
Sometimes emissions cannot be entirely removed, and so in these situations, it is far easier to absorb them before they get to the outside world. This is mostly done using Faraday cages that either surround noisy components or an entire product, and the shield is often connected to a ground (i.e. 0V on the internal circuit).
Metal shielding is commonly found on Wi-Fi and Bluetooth SoCs that are directly soldered to PCBs. The metal shield surrounds the main IC as well as its supporting components and is often soldered to ground. The antenna is a PCB trace that goes beyond the metal case to an area of the board that has its ground planes removed.
Absorption of emissions can also be done using power planes on a PCB. For boards that have more than two layers, the two innermost layers are often used as power planes (one layer ground, the other power), and these can be effective at absorbing stray emissions. The most outer layers are often reserved for signals, and even these layers will include ground pours. From there, stitching via can be used to surround exceptionally noisy circuitry (such as power handling areas), and these stitching via help to create Faraday cages.
Conclusion
EMC is not an easy feat to accomplish, and this article merely provides a brief introduction to the causes of emissions and how to fight back against them. Engineers need to consider EMC at all stages of circuit design, and the earlier EMC is considered in a project, the easier it is to develop. Projects that don’t consider EMC until the end can often result in a complete redesign costing both time and money.
Read More
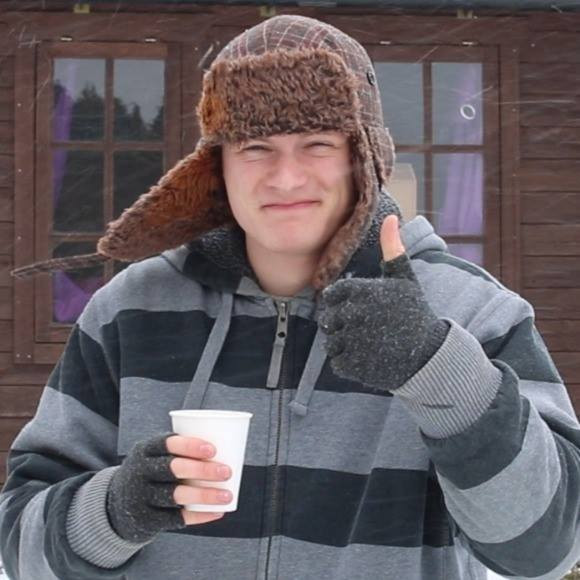