Semiconductors – Why they could be impossible in India and why so few places make them!
Semiconductors | 02-08-2020 | By Robin Mitchell
Last week, the government of India asked for a production plant in India, but some say that this is close to impossible. Why is this the case, and what makes setting up semiconductor foundries a tricky business?
India’s Desire for Semiconductors
India is one of the most populated places in the world with over a billion, and its growing economic power makes it a desirable market for selling electronics. For perspective, if even just 1% of the population demanded the next generation of smartphones, that would be over 10 million customers for a phone that could cost more than $400 each. While India does design and manufacture electronics, all integrated circuits (that’s right, ALL, not most), are imported into the country with China being a major supplier. Recent tension between India and China does not help, which is why the Ministry of Commerce and Industry is looking to encourage the introduction of semiconductor foundries. However, despite numerous attempts to do so, these foundries either fail at the start or become partially successful, only to fail as a result of government action. Two foundries do exist in India, SITAR and DRDO, but these only produce devices for use in strategic applications such as defence. So, what components are semiconductor industries dependent on, and why is it hard to enter the market?
Read More
Semiconductor Precursors
While some may disagree, producing semiconductor devices is far more straightforward than you would think, and the precursor chemicals and compounds are widely available. This has been demonstrated where makers have created their own semiconductor devices at home, with one individual having made a fully working integrated circuit with individual components on a single chip! (Think “Tony stark made this in a cave, with a box of scraps”). If semiconductor technology were inherently complex, then it would have been incredibly difficult to establish in the past. So, what are the basic processes to semiconductor manufacture?
Semiconductor production falls into three main areas; silicon wafer creation, circuit construction, and packaging. The creation of silicon wafers is a complex task as it requires careful temperature control and drawing of the single crystal ingot at 1000°C. If the crystals are drawn out too quickly, or the temperature variance is greater than ±1°C, then the crystal will either be unusable or produce low yields. One created, the ingot is cut to size and then diced up into individual plane wafers. This is where the second stage steps in.
Integrating a circuit onto a silicon wafer involves lots of repeated steps as each layer is built up one by one. The first layer is what defines the transistor devices themselves (creating P and N regions), while the layer above this defines gates and interconnects to the layers above. After this, each layer above is used to route signals in metallic layers that connect all the components to create an integrated circuit. The top layer brings out the I/O to the circuit onto large metallic pads which is what the last step utilises.
The last step takes a wafer, splits it up into individual die, and then mounts them into their IC packages. From there, wires are bonded from the metal I/O pads on the die to pads on the IC package which then carries those connections to pins on the package.
While there are many precursor products needed to produce semiconductors, most are commonly available components including
-
Hydrofluoric, hydrochloric, and sulphuric acid
-
UV exposable etch resists (used in the PCB industry)
-
Metals including aluminium, tin, and gold
-
Inert gasses such as Nitrogen
-
Oxygen for oxide growth
So, if producing semiconductor circuits uses easily obtainable chemicals, why is it so difficult to set up a foundry?
Read More
70 Years Too Late
Unlike many other industries, semiconductors are always under change, and the physical size of transistors keeps reducing. This constant reduction in size, often referred to as Moore’s Law has seen transistors in the millimetres shrink down to the nanometres. Producing semiconductors from the 1970s is an easy task by modern standards, but these devices would only hold a handful of transistors in large bulky packages that would not be useful in contemporary design.
Older semiconductors are easy to produce for a whole range of reasons, but one of the most significant factors that make it challenging to produce modern semiconductors comes down to shrinking the image of the design onto the wafer. In the past, this was done using a collimated light source which would be shone through a large pattern, and a lens to shrink the image down. However, as the size of the features on a die became smaller than the wavelength of the light being used, designers had to cope with diffraction and interference. Modern methods for getting patterns onto a die are incredibly complex, and only a handful of companies globally can do this. Thus, any company wanting to start their foundry has 70 years of technological development to catch up on. This problem is amplified if a company wants to start with constructing modern devices immediately; high-end equipment needs to be purchased, which can cost billions of dollars.
Read More
Conclusion
Semiconductor devices have come a very long way since the creation of the first transistors. Now that features are approaching the single nanometre sizes, only a handful of companies around the world can produce these devices. Increasing tension with China may see countries around the world try to become self-sufficient in electronics technology, but it will be a tough industry to enter, and success is never guaranteed.
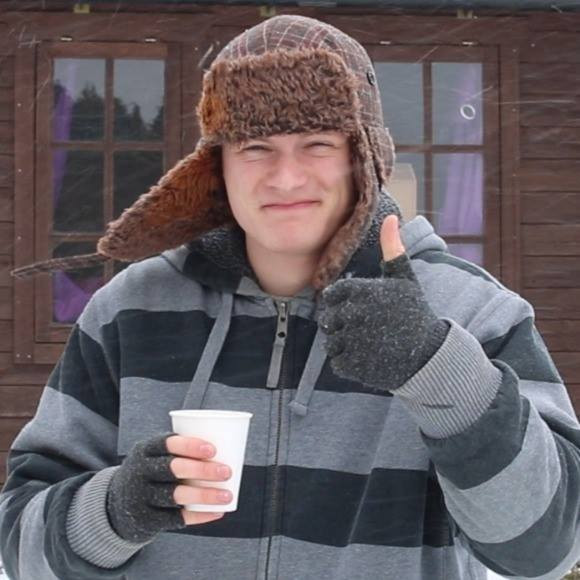