Decentralised systems for ‘next generation’ industrial production
| 13-06-2019 | By Nnamdi Anyadike
As industry moves into the ‘next generation’, or Industry 4.0 production process, ‘smart’ decentralised plant control will inevitably become its distinguishing feature. Decentralised control will simplify the manufacturing process and provide the manufacturer with a greater overview of the entire production chain. Industry 4.0 promises to integrate cyber-physical systems (CPSs), computation, networking, and physical processes into a seamless whole. Its basic design principles will include interoperability; information transparency; human-machine interaction and decentralized decisions. This more modular, flexible and autonomous approach to production will require new systems with decentralised intelligence, which can cope with the increasing complexity of the processes.
Major players operating in the industrial control and factory automation market, as identified by a recent ‘marketsandmarkets.com’ report, are Emerson (US), ABB (Switzerland), Siemens (Germany), General Electric (US), Schneider (France), Endress+Hauser (Switzerland), Yokogawa (Japan), Honeywell (US), WIKA (Germany), Azbil (Japan), Fuji Electric (Japan), 3D Systems (US), HP (US), FANUC (Japan), STRATASYS (US), Progea (Italy), Hitachi (Japan), Vega (Germany), Danfoss (Denmark), Tegan Innovations (Ireland), Krohne (Germany), Rockwell (US), Chaos Prime (US), and Dwyer (US).
Field drive system that ‘thinks’ with you
MSF-Vathauer Antriebstechnik GmbH & Co KG, the German-based manufacturer of decentralised drive automation, claims to have developed Field Drive System®, a field drive system “that thinks with you.” The company claims that the decentralized motor management system will simplify the production process and provide both the user and the machine manufacturer with more clarity, flexibility and greater freedom. Managing Director Marc Vathauer said, "Machine manufacturer projects are implemented faster and the downtime of the machine user is reduced. In the case of maintenance, the system availability for the user is considerably increased with the Field Drive System®." Standardized sensor connections connect the sensors directly to the starting motor and to the frequency converter at no extra cost. The system can be connected via other connection technologies to all energy bus systems available on the market.
NORD DRIVESYSTEMS’ decentralised drive technology
NORD DRIVESYSTEMS, one of the major leaders in drive technology worldwide for mechanical and electronic solutions, has developed decentralised drive units that can be flexibly integrated into the plant. Decentralised frequency inverters offer many advantages: They save space in control cabinets, reduce cable and wiring costs, simplify maintenance and therefore increase the efficiency of the entire drive system. The company has an extensive range of modular products for decentralised drive electronics, which can be integrated into all automation architectures. The drive units are networked, autonomous and scalable. ‘NORDAC LINK’ enables fast commissioning, simple operation and maintenance, while ‘NORDAC FLEX’ is the most flexible NORD inverter. It is easy to service and comes with a power range of up to 22kW. The company claims, “Thanks to their modular structure, NORD inverters can be easily extended and offer an impressive variety of scenarios for use in Industry 4.0 automation networks. Their ‘fields of use’ range from conveyor technology and intra-logistics, to drive tasks in the packaging and food industries as well as pump applications and general mechanical engineering.”
TI Sitara Processors’ smarter servo drives
Meanwhile, the Sitara family of microcontrollers from Texas Instruments has unveiled ‘Sitara AM6x’ that is designed for Industry 4. The TI web site says, “Servo motors have been a staple in manufacturing and automation for many years. Now, though, with the rise of Industry 4.0 and smart factories, demand is increasing for smarter servo drives that can control a greater number of axes.” Several TI processing solutions are suitable for servo-drive applications, including Sitara, Hercules, and C2000 controllers. But the AM65x will also accommodate Industry 4.0 functional safety, security, networking, and communication requirements. Enhanced connectivity is central to the AM6x design. It comes with three next-generation industrial communication systems (ICSSs), each containing four programmable real-time units (PRUs) running at up to 250 MHz. Some unique investments made in the AM6x processor design were to enhance reliability and to provide the ability to reach higher levels functional safety. The processing solution also comes with extended life. The company explained, “The AM6x provides at least 10 years of operation at maximum junction temperature with extended longevity estimates for customers interested in longer lifetimes for their systems.”
Outlook
Marketsandmarkets.com expects the industrial control and factory automation market to reach $269.5 billion by 2024, from $160.0 billion in 2018. This represents a healthy CAGR of 9.08%. Industrial robots are expected to be the largest contributor in components of the industrial control and factory automation. Recent developments include: the GE and Microsoft Corp. partnership to bring together operational technology and information technology; the SAP and Endress+Hauser collaboration in the development of the Industrial Internet of Things (IIoT) applications for the process industry; and the ABB and IBM partnership for industrial artificial intelligence solutions to improve the production lines by identifying critical faults during the manufacturing process.
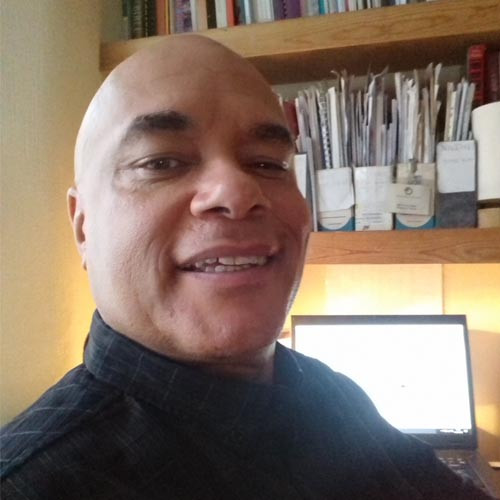