Amazon AI Foundation Model Drives 1M-Robot Deployment
Insights | 10-07-2025 | By Robin Mitchell
Key Takeaways:
- Amazon has deployed over one million robots across more than 300 fulfilment centres, signalling a major shift in how large-scale logistics are powered.
- DeepFleet, a new AI foundation model, improves robotic movement efficiency by 10%, contributing to faster delivery times and reduced operational costs.
- The shift toward automation is widening the skills gap, with technical roles replacing low-barrier jobs, creating long-term implications for labour accessibility.
- Amazon’s upskilling efforts have supported 700,000 employees, but questions remain around the inclusivity and scalability of these programmes.
While automation has long been a feature of industrial progress, recent breakthroughs in AI and robotics are accelerating a shift unlike any before. What was once considered experimental is now quietly transforming workplaces, reshaping the labour market, and redefining what it means to be employable in a digital economy.
What forces are driving this new wave of automation, how is a company like Amazon leading the charge, and what does this mean for the future of work in a world where machines are no longer assisting, but replacing, human roles?
The Emerging AI and Robotic Issue
For decades, robotics and artificial intelligence have been viewed as experimental technologies that are fascinating but far from practical in day-to-day industry. Early versions were limited in scope, expensive to implement, and typically reserved for narrow, niche applications. They posed no real threat to human jobs. That era is over.
Today, AI and robotics have advanced to a point where they're no longer experimental; they're operational. Across industries, they are being deployed not just as tools to assist workers but as direct replacements for them. And unlike previous industrial revolutions, this one appears to be creating fewer jobs than it eliminates.
The early generations of AI were nothing to worry about, barely competent, slow, and brittle. They couldn't generalise or adapt. Robotics, too, was confined to structured environments with strict repeatability. But over the last decade, improvements in machine learning models, edge computing, and sensor integration have brought AI and robotics to a functional maturity. They're now good enough to take over tasks that used to be handled by junior employees or skilled tradespeople.
From Technical Breakthroughs to Job Displacement: The New Reality of ‘Good Enough’ AI
The first casualties are entry-level positions. AI now drafts emails, handles customer service, analyses simple data, writes code, and even generates marketing copy. It doesn't do it perfectly, but it doesn't have to. In many cases, "good enough" is enough to cut costs. And on the robotics side, factories are increasingly using autonomous systems for everything from picking and packing to inspection and maintenance. These machines run 24/7, don't require breaks, and don't make HR complaints.
The concern is not just automation itself, but the nature of this particular wave. Historically, disruptive technologies created new types of work to replace the old. The internet replaced paper, but gave rise to whole new industries. The problem with the current shift is that the jobs being created require far more technical skill and training than the jobs being lost. In other words, the barrier to entry is going up, not down. And that leaves a growing number of workers stranded, skilled in roles that no longer exist, and unqualified for the new ones.
We're already seeing companies reduce the number of entry-level positions. AI tools have taken over the basic tasks that used to justify junior hires. As a result, even so-called "entry-level" jobs now demand prior experience. The traditional path of working your way up is narrowing. We are witnessing the early phase of a broader transformation, one in which AI and robotics will reshape not only how we work, but who gets to work in the first place.
The trend is in motion. The question now is how long before it becomes irreversible.
Amazon's One-Millionth Robot and the Rise of DeepFleet AI
If there were any doubts about where the future of industrial labour is headed, Amazon just put them to rest. On June 30, 2025, the company announced two significant milestones: the deployment of its one millionth robot and the launch of a new generative AI foundation model called DeepFleet. Together, these developments mark a turning point not just for Amazon, but for the broader conversation around automation, jobs, and the future of work.
DeepFleet’s architecture reflects a broader evolution in warehouse AI systems, moving from reactive to predictive models. Using a vast repository of historical inventory data and AWS technologies such as SageMaker, the system anticipates potential bottlenecks and proactively adjusts robot paths. This predictive capability supports large-scale fulfilment logistics and reinforces Amazon’s commitment to maintaining global operational continuity.
From Reactive Routing to Predictive Optimisation: How DeepFleet Rethinks Warehouse Mobility
DeepFleet is Amazon's latest leap forward, designed to optimise robot movement across more than 300 fulfilment centres worldwide. The result? A 10 percent increase in robot travel efficiency. That may not sound dramatic at first glance, but in a system of one million autonomous units, 10 percent is massive. It means faster deliveries, lower operational costs, and even less dependence on entry-level human labour.
According to Amazon, DeepFleet reduces robotic travel time by 10%, which has a direct impact on energy consumption and carbon emissions. While not publicly quantified, these marginal efficiency gains compound across Amazon’s global network of over 300 sites, supporting the company’s sustainability goals. In this light, DeepFleet operates not only as an automation optimiser but also as a low-profile contributor to environmental efficiency strategies.
Efficiency Meets Sustainability: The Environmental Impact of Smarter Robotics
From a technical standpoint, DeepFleet is essentially a highly advanced traffic control system, built using Amazon's massive warehouse data and powered by in-house generative AI tooling. It learns from real-world operations and continuously refines robot paths in real-time. It's the kind of system that doesn't just replace human decision-making, it eclipses it.
From a systems perspective, DeepFleet functions similarly to a dynamic routing platform, comparable to an urban traffic system that evolves with live input. This model is particularly well suited to warehouse environments where minor inefficiencies can ripple into major delays. The system's iterative learning loop enables near-continuous refinement, helping Amazon approach high availability and fulfilment resilience thresholds that were previously unattainable without human oversight.
Collaborative Automation or Strategic Displacement? The Workforce Perspective
Scott Dresser, VP of Amazon Robotics, emphasised that robots are not replacing workers, but working alongside them. It's a comforting narrative, and to some extent, it holds water, Amazon has upskilled over 700,000 employees through internal programs since 2019, with many now focused on maintaining and supervising these robotic systems. But let's keep perspective: not everyone laid off from a repetitive task role will suddenly pivot into robotics maintenance or data analytics.
Amazon’s upskilling initiatives are underpinned by programmes like Career Choice, which subsidises technical education for warehouse staff. The shift from manual to maintenance roles is part of a broader workforce transformation strategy aimed at creating long-term employment viability within highly automated environments. However, it remains unclear what percentage of the workforce ultimately transitions into these new roles successfully, highlighting an area requiring further transparency.
Upskilling vs. Accessibility: Who Really Benefits from AI-Driven Workforce Shifts?
Despite claims that AI is creating new job categories, the numbers suggest a different trend: more automation, fewer low-barrier job openings, and increased demand for specialised technical expertise. Amazon's own next-generation fulfilment centre in Louisiana reportedly requires 30 per cent more engineering and maintenance staff than previous designs. That sounds like a win, but again, it's a win for trained specialists, not for displaced warehouse workers without a technical background.
The company's own data shows a growing reliance on technical staff in robotics-heavy fulfilment centres. In Shreveport, Louisiana, for example, Amazon's latest site design demands 30% more personnel in roles like reliability engineering and AI systems support. While this indicates a strong demand for skilled labour, it simultaneously underscores the growing divide between accessible warehouse jobs and those requiring post-secondary technical education.
Engineering Demand Rises, But So Does the Skills Gap
At the surface level, Amazon's robotic fleet is a marvel of engineering and logistics. But dig a little deeper, and it also illustrates the broader concern: this generation of automation is different. It doesn't just make human labour more productive, it renders large chunks of it unnecessary. And while Amazon's investment in U.S.-based manufacturing and employee training is commendable, it's also strategic. The optics matter. A fully robotic future still makes people uneasy.
To address these optics, Amazon has invested in domestic manufacturing for its robotics programmes, partnering with local suppliers to maintain a robust quality-control feedback loop. This localisation strategy supports economic development narratives and strengthens Amazon’s ability to adapt quickly to feedback from its operations teams. Whether this will satisfy concerns around workforce displacement remains an open question, but the optics around decentralised production are clearly part of the company’s strategy.
What This Means for the Future
On paper, the statistic that Amazon has upskilled 700,000 employees looks impressive. It's certainly the number they want in the headlines. But put that next to the fact that they've deployed over one million robots, and the story changes. That ratio tells you everything you need to know: the balance between machines and people is tilting fast, and not in favour of human labour.
Being realistic, those one million robots didn't just show up to "assist" workers. They replaced them outright. Quietly, incrementally, and permanently. Even if only half of them displaced full-time roles, we're still talking about hundreds of thousands of jobs removed from the economy. And no matter how many glossy training programs a company offers, the math doesn't lie: more automation means fewer employment opportunities, especially for those entering the workforce.
Yes, efficiency improves. Yes, operational costs drop. But those gains come with a cost, and it's not paid by corporations. It's paid by the people left behind. Economic stability depends on employment. You can't have a functioning economy if the bottom half of the population is locked out of the labour market, stuck behind an ever-rising skills barrier. Technology is supposed to serve people, not the other way around.
The Hidden Cost of Efficiency: Economic Displacement at Scale
There's this persistent myth that automating everything is inherently good for the economy. That's only true if displaced workers find new jobs, start businesses, or move into more productive sectors. But if all we're doing is cutting headcount and tightening hiring requirements, we're not building anything. We're just concentrating wealth and stripping mobility from the next generation.
If a young person today can't land a job because a robot took it and the remaining roles require a degree, certifications, or specialised technical skills they don't have access to, they fall behind. Permanently. That's how poverty cycles begin, and deepen.
As someone who's been a champion of technology my entire career, I'll admit this trend is deeply concerning. I'm not anti-innovation. I'm anti-collapse. If we're not careful, we're setting ourselves up for a future where efficiency outpaces humanity, and there won't be a simple patch or software update to fix that.
This conversation needs to happen now. Not five years from now, not when unemployment numbers start trending in the wrong direction. We're already seeing the warning signs. The question is whether anyone's actually paying attention.
Dare I say, do we need the forbidden G word to step up, take control over AI, and regulate the industry? Does...government...need to get involved?
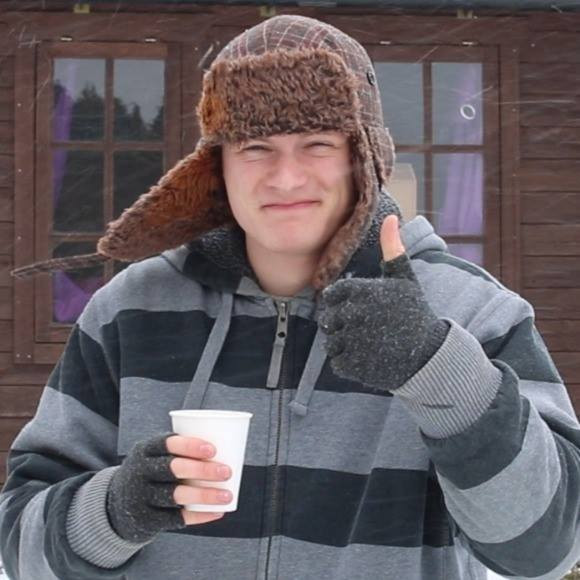