Silicon Carbide and Gallium Nitride for EV Power Efficiency
Insights | 06-06-2024 | By Gary Elinoff
Wide Bandgap Semiconductors deliver the power for EVs. Image source: Infineon
Key Takeaways about Power Semiconductors for Electric Vehicles:
- Generating the energy needed by EVs isn’t without ecological consequences.
- The employment of Wide Bandgap semiconductors, such as Gallium Nitride and Silicon Carbide within EVs makes them as electrically efficient as possible.
The use of Wide Bandgap semiconductors within EVs allows them to require less power from the grid, underpinning a greener future.
Introduction
One of the key underpinnings of today’s push towards lowering CO2 emissions, saving energy and conserving our environment is the advent of the Electric Vehicle (EV). The power that animates EVs is, of course, electricity, and if the EV is to live up to its hype as an ecological superhero, it needs to sip as little power from the grid as possible. To do that, it needs to use energy as efficiently as possible. Its wide bandgap semiconductors (WBG), such as gallium nitride (GaN) and silicon carbide (SiC), make that possible.
But before we take a deeper dive into just what WBGs do and how they do it, let’s take a short excursion into two automotive ecosystems.
Gasoline vs Electricity
If you think that EVs have an unfair advantage – you’re right! Before anything else, electrical motors are just plain more efficient than gasoline motors.
There’s something else that’s even more profound. Just look under the hood of even the most powerful vehicle from the 1960s – you can actually see the pavement under the vehicle! If you make the same observation in a modern gas vehicle, you won’t see the ground but instead a frightening array of pumps, tubes, vents and whatnot – a chemical engineer’s paradise devoted to nothing other than pollution control.
That’s all missing in EV’s
Electric motors don’t generate pollution like gasoline engines do – no pollution control system is needed. ALL the hydrocarbon pollution control is taken care of at the source - the power plant. Instead of the many millions of gasoline-powered cars, each supporting a complex, energy-hungry automatic pollution control system, there need be only one such system, at the power plant itself, constantly monitored by both human experts and advanced automation. The end result is one supremely efficacious system replacing millions of less effective vehicle-based arrangements.
The EV’s Gas Tank
The EV’s “gas tank”, its reservoir of power, is the lithium Ion Battery(LiB), and it stores perhaps 150 kilowatt hours of DC electricity at 800 volts. The problem is that very little in the car runs at 800 volts DC.
The main motor runs at AC voltages in the range of 400 to 800 VAC. There are a myriad of other devices that require a dizzying range of voltages. This conversion process is at the heart of what makes an EV tick. WBGs can do so far more efficiently than classical silicon (Si) semiconductors can.
So, How Do Wide Bandgap Semiconductors Do It?
Imagine accessing a LiB’s voltage through a switch. As the switch is turned on and off, pulsating DC is derived. Through pathways well-known by electrical engineers, pulsating DC can be converted to a wide range of AC or DC voltages. The key to it is the efficacy of the switching, as well as how well the device handles heat.
Let’s take a look at how GaN and SiC stack up compared to legacy Silicon (Si) semiconductors.
Faster Switching. When converting DC to another voltage level of DC, the WGB is directed to switch ON and OFF many thousands of times a second, creating pulsating DC, and the faster the switching, the closer the pulses are to each other. The process of converting these “pulses” to the clean, stable DC requires a “filter” consisting largely of inductors and capacitors. The higher the frequency of the pulses, the smaller the filter components can be. This saves a great deal of weight and space, and similar benefits are gained when converting DC to the AC needed by the main “tractor motor” that substitutes for the gasoline motor of a conventional vehicle.
WGB semiconductors can switch far faster than silicon devices can.
Lower “ON” Resistance. Power semiconductors are often referred to as switches, and an ideal semiconductor, like an ideal electromechanical switch, must present a resistance as close to zero as possible. If there’s any resistance, voltage crossing resistance generates heat and wastes power. The resistance across the semiconductor, the resistance between the device’s “source” and “drain”, is referred to as the RSD(ON).
And here, too, WGBs beat Si devices hands down.
Heat. But while WGB semiconductors operate more efficiently than Si devices, inevitably there is some inefficiency, causing heat to be generated. But WBGs can actually tolerate more internal heat and still operate safely and efficiently. Additionally, WGB thermal conductivity is greater, making it easier to dissipate parasitic heat away from the semiconductor.
What are the main Characteristic Differences between GaN and SiC?
There are two differences that stand out and are of crucial importance to EV designers. Basically speaking, SiC can handle more power, but GaN can switch faster. The sands are constantly shifting, but this classical diagram tells the story.
GaN vs SiC vs Silicon. Modified Image source: AVNET
However, there is one axis on which WGBs come out the loser, and that’s cost, especially for SiC.
One of the central features of an EV is the drivetrain inverter, the semiconductor based device that converts the LiB’s DC voltage to the constantly varying AC waveforms required to power the EV’s main motor. For more powerful EVs, higher power SiC semiconductors are the clear technical choice. But as we shall see, the high cost of SiC devices are a major impediment.
Tesla’s SiC Issues
As reported by PSG Consultancy[1], Tesla was the first EV manufacturer to adapt SiC technology for a drive train inverter. Aimed the manufacturer’s ubiquitous Model 3, it was “a catalyst for a massive expansion of the SiC industry”. We might also add that it had implications well beyond the transportation industry.
Then, in 2023, Tesla dropped a bombshell when it announced a planned 75% reduction of SiC usage. It was thought that they might employ lower cost GaN devices, or maybe even revert to last generation Silicon IGBTs.
Some insight can be gained by taking a look at the assumed insides of the Tesla Inverter.
This is the basic diagram for a DC-to-AC converter. Each leg of the Model 3’s inverter employs eight 650V SiC MOSFETs from STMicroelectronics deployed in parallel. That’s a total of 48 semiconductors. Expensive, but its enhanced efficiency as compared to previous drive train inverters enabled the Model 3 to travel further without increasing LiB capacity, size or weight.
But there might be less to the announcement than meets the eye.
- Better positioning within the chassis of the inverter will allow SiCs to dissipate more heat so each semiconductor can be pushed further, eliminating the need for eight on each leg.
- Vast amounts of money are being spent on SiC development. More capable semiconductors will mean fewer are needed.
- The eventual transition to 800V systems. The higher the voltage, the less current and heat
- New models might deploy less powerful motors, needing proportionally fewer SiC semiconductors.
However, the rapid advancement of cheaper GaN technology may, in some design cases, make it possible for that technology to substitute for SiC.
Gallium Nitride Power Semiconductors for both 400V and 800V EV Systems
As reported in a previous Electropages article[2], “While GaN-on-silicon leverages existing infrastructure and is typically limited to 650V, the advent of GaN-on-Qromis-substrate-technology (QST) allows for thicker epitaxial layers. This innovation enables operation at higher voltages, potentially up to 1,200V or more.”
This puts GaN semiconductors in line to power almost any present EV and just about any now on the horizon. And of singular importance, SiC devices are far harder to manufacture, which is, of course, reflected in their higher costs.
Most importantly, GaN switching speeds are high compared even to SiC, let alone to classical silicon. This argues for greater efficiency, as well as lower weight and space requirements.
For these reasons and more, GaN is going to give SiC a run for its money, especially for lower-priced, mass-market EVs
Challenges and Opportunities
The largest impediment to massive EV adaptation is the lack of charging infrastructure. Seeing the handwriting on the wall, gas retailers are making the logical move into providing for profit (of course!), charging for the motoring public.
By most measures, the efficiency of the pathway between the charging station to the EV’s wheels is well over 90% even now. The last great frontier is the LiB itself. Scientists and engineers in the US, Europe and East Asia are pouring over the problems, the most critical being how long it takes the device to charge.
While EVs may have been the initial catalyst spurring WGB development, other areas of technology are not only reaping the benefits but are also contributing to development. Areas include:
- The server farms already serving the internet need a well-regulated supply of power, as well as the exponential growth that server-based artificial intelligence will demand.
- Solar and wind power
- The smart grid
- MRI machines and CT scanning
- Radar systems
- Missile technology
Wrapping Up
Wide bandgap semiconductors switch faster, have lower “ON” resistances, and handle heat far better than last-generation silicon devices. They can be found across the whole gamut of electrical and electronic devices – everything from tiny medical wearables to the largest electric vehicles.
Two of the main differences between SiC and GaN semiconductors are that SiC can handle more power, while GaN switches faster and is cheaper. And of critical importance, GaN is easier to manufacture and is consequently less expensive to OEMs.
The previous limitations on the power that GaN devices can handle and in the voltages at which they operate are being gradually overcome, allowing them to challenge SiC’s previous domination in high power EV applications.
References:
- Examining Tesla’s 75% SiC Reduction: https://www.pgcconsultancy.com/post/examining-tesla-s-75-sic-reduction
- The Band Gap Showdown: GaN or SiC - Which Will Prevail?: https://www.electropages.com/blog/2024/01/what-will-win-battle-bandgap-gan-or-sic
Glossary of Key Terms:
- Wide Bandgap Semiconductors (WBG). A fast-expanding subset of semiconductors that offer considerable advantages as compared to classical silicon-based devices
- Lithium Ion Batteries (LiB). These now ubiquitous devices are noted for their rechargeability and for their high energy density.
- Traction Inverter. A device that converts the EV’s LiB’s DC voltage to the varying AC needed to power the vehicle’s main motor
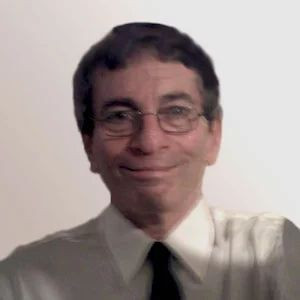