Space vs. Earth: Where Will the Next Semiconductor Revolution Occur?
Insights | 11-09-2023 | By Robin Mitchell
As technology continues to progress, some look to space for the next industrial revolution. What challenges does manufacturing on Earth present, how could space-based manufacturing help, and is it feasible?
What challenges does manufacturing on Earth present?
All technology humanity has ever developed depends entirely on our planet’s natural forces. Iron that cools down slowly becomes magnetic due to the Earth’s magnetic field. Gravity causes fluids of different densities to separate into layers due to gravity, and many materials oxidize due to the presence of oxygen in Earth’s atmosphere.
In most cases, humanity has learned to cope with these natural phenomena and use them as an advantage. For example, magnetic materials as a result of the Earth’s magnetic field have allowed for the creation of compasses, while gravity has helped with the distillation of petroleum, the casting of metal, and even as a means to slowly draw crystals through induction heaters (see history of semiconductors in Japan).
However, for all the benefits that manufacturing on Earth presents, there are a number of challenges that face engineers. To start, the contents of the atmosphere are perfect for life but not for many manufacturing processes, especially those involved with combustible materials and metals. In cases of potentially explosive environments, oxygen needs to be purged with the use of inert gasses (such as nitrogen), which can be tricky to contain. With regards to oxidisation, it is also possible to use inert gasses, but this is not only expensive but can be difficult when working at scale (such as trying to prevent a one-ton piece of iron from oxidising).
Additionally, the presence of air can also interfere with advanced manufacturing techniques such as chemical vapour deposition and ion beam deposition. In these cases, a vacuum is required, resulting in the need for vacuum chambers and pumping equipment. These requirements make such manufacturing techniques extraordinarily expensive and, thus, inaccessible to most engineering projects.
Gravity can also be problematic, especially in the forming of crystalline structures used in semiconductors. As gravity causes liquids to move around while simultaneously subjecting each molecule to a downward force, crystals can form unevenly, resulting in grain boundaries forming.
In a more extreme case of gravity affecting processes, studying protein structures is critical in the manufacture of pharmaceuticals, but proteins in solution that are dried out collapse and become misshapen under the influence of gravity. If crystallised in a micro-gravity environment, the structure of the protein can be preserved, thereby giving researchers a better understanding of the protein’s behaviour.
Numerous other environmental factors can also introduce difficulties in manufacturing. One such example is in the area of geological instability, whereby small tremors in the ground can affect the manufacturing of high-tech systems. Another such example is weather patterns that can introduce extreme heat, extreme cold, high winds, and torrential floods.
According to a recent NASA news release, the potential of space-based manufacturing is being explored in depth. NASA's focus on innovative space technologies aligns with the idea that space can offer unique environments beneficial for manufacturing, which Earth cannot provide.
“NASA is excited to begin collaboration with these new partners in our efforts to enable development of a robust commercial economy in low-Earth orbit,” said Kevin Engelbert, In Space Production Applications portfolio manager. “Enabling proof-of-concept demonstrations on the International Space Station National Lab is a first step towards future production of important new materials and products that will benefit people everywhere on Earth, while strengthening U.S. leadership in advanced materials and manufacturing in space.”
How space-based manufacturing could help
As the cost of space launches continues to fall, thanks to a multitude of emerging technologies, engineers and researchers are starting to ponder whether manufacturing in space could soon become a reality. While the idea of manufacturing in space sounds cool, there are some very real benefits to working in microgravity environments.
The semiconductor industry is one such sector that could see major benefits as a result of space-based manufacturing. To start, the minimal effects of gravity (remember, there is still gravity in an orbit around Earth; it’s just that by constantly falling, it appears that there is no gravity) can help with the formation of high-quality crystals, thereby improving the capabilities of semiconductors.
The lack of an atmosphere also introduces a major advantage to production stages that require a vacuum. In fact, as space is entirely empty, there is no cost associated with scaling up manufacturing processes relying on vacuums, thereby reducing the costs. This also eliminates the need for controlled pressure vessels capable of withstanding vacuum pressures.
Due to the extreme stability of orbits (and lack of tectonic activity), space environments are free from all vibrations, meaning that manufacturing extremely delicate and small features is far easier to accomplish. The large distance between orbiting bodies and civilisation also introduces the possibility for extremely controlled environments with regard to EM radiation such as radio, but the high intensity of cosmic rays will introduce its own range of challenges.
Finally, if asteroid mining were to ever become viable, it would tie in well with space-based manufacturing as there would be no need to move raw materials from Earth. Thus, an entire manufacturing ecosystem could exist solely in space, with finished goods being sent down to Earth via gravitational pull.
The UK Government's Space Exploration Technology Roadmap also highlights the potential advancements in space technology, suggesting that as we develop more sophisticated space exploration tools, the feasibility of space-based manufacturing will increase.
Is such a concept feasible?
Considering that there are vast resources easily accessible on planet Earth, space-based manufacturing is far from being economically feasible and will unlikely be so for centuries to come. However, as humanity begins to journey out into the solar system, it is possible that space-based manufacturing will become highly convenient, eliminating the need for fuel and reusable rockets that experience massive forces during take-off and landing.
Space-based manufacturing may also be economical should humanity start developing more space stations. Even trivial manufacturing techniques such as 3D printing could be ideal for situations when trying to ship a small bracket from Earth is too expensive.
In fact, it is most likely that future space stations will have manufacturing hubs and cargo from Earth, mostly containing raw 3D printing filaments. By doing so, engineers onboard space stations can make exactly what they need when they need it.
The same can be said for small-scale PCB manufacturing systems, where component reels are sent to a space station for later use instead of trying to provide fully built circuits designed for specific applications. By allowing engineers to manufacture exactly what they need, they can make the most of their resources while minimising waste from resupply missions from Earth.
There is no doubt that space-based manufacturing can provide substantial benefits, but as technology and economies currently stand, it will be unlikely in our lifetimes.
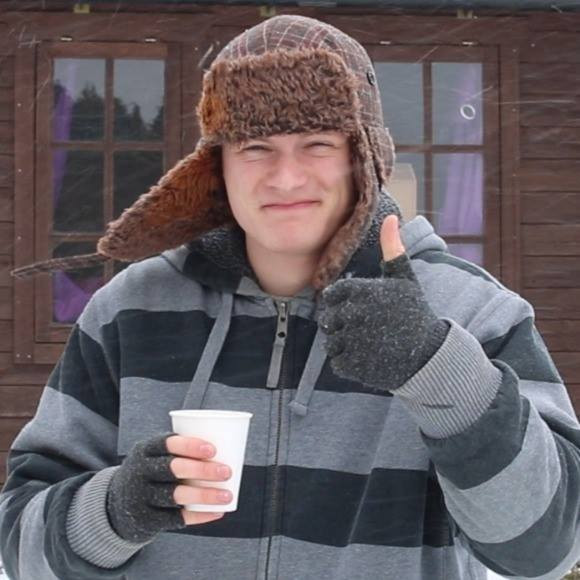