How Printed Electronics are Shaping the Future of Space Exploration
Insights | 29-06-2023 | By Robin Mitchell
As the space industry continues to grow, engineers routinely look for methods to reduce the weight of payloads going into space, whether it is new materials or unique design concepts. Printed electronics is one area of interest that could help minimise payload weight. What challenges do payloads face when reaching orbit, how could printed electronics help, and what challenges would printed electronics face?
What challenges do payloads face when reaching orbit?
Getting anything into space has never been an easy challenge; space is far away, the atmosphere introduces all kinds of complex aerodynamic issues, and making rockets bigger to carry larger payloads doesn’t scale entirely well (in that additional rocket weight needs more fuel, thereby needing a larger rocket). In fact, it has taken decades of research and experimentation just to get a rocket to be partially reusable, and even then, such rockets need to undergo expensive and time-consuming checks and maintenance.
However, it is not just the rocket that needs to be designed carefully; even payloads need a great deal of consideration. So, what are these considerations, and how do they affect a design?
The biggest consideration by far is weight, as sending anything into space is extraordinarily expensive. Considering that sending 1KG into space can cost around $12,000, engineers must consider every gram that is being sent. For example, if an enclosure for a CubeSat can be reduced in weight by 100g, not only is the launch cost reduced, but the saved weight can be better used in electronics, sensors, and other useful components.
As such, it is common to find engineers opting for lightweight materials or to utilise unique design concepts that eliminate as much material as possible. The same applies to electronic circuits; the use of smaller connectors, smaller IC packages, and smaller passives all help to reduce the overall weight.
The second major consideration is the forces that will be exerted during lift-off. Due to the rapid rate of acceleration of rockets during early flight and the complex aerodynamics between the rocket and atmospheres, payloads can be subject to extremely harsh vibrations and shock, all of which are very capable of causing damage. Thus, engineers have to put their payloads through rigorous testing to ensure that their designs will survive the journey to space.
The third major challenge that engineers need to consider is redundancy. When in space, performing physical maintenance is a virtual impossibility (especially now that the Space Shuttle has been retired), meaning that anything placed into orbit needs to be able to have fallback options to continue operation. For example, it is not uncommon for a satellite to have multiple redundant systems, such as additional processors and memory banks, that can all be swapped around in software so that a failure in one doesn’t knock the satellite out of commission.
Could printed electronics help with reducing payload weights?
One technology that could help engineers solve problems faced by designs going into space is printed electronics. Unlike traditional electronics manufactured from bulky components mounted onto a PCB, printed electronics are generally entirely manufactured using specialised inks that are printed onto surfaces layer by layer.
The use of additive manufacturing not only allows for custom components to be printed but also allows for printing electronics onto most surfaces and substrates, including flexible materials. So, how could printed electronics help with space-based applications?
Thin and Lightweight Circuits
One of the key advantages of printed electronics lies in its ability to create thin and lightweight circuits. Traditional rigid circuit boards can be replaced with flexible, printed circuitry that conforms to the shape of the payload. By eliminating bulky components and minimizing wiring, the overall weight of the payload can be significantly reduced. The flexibility of printed electronics also enables complex circuit designs to be integrated into unconventional shapes, optimizing space utilization.
Integration of Sensors and Actuators
Printed electronics, unlike traditional electronics, allows for the integration of various sensors and actuators directly onto the payload structure, eliminating the need for separate components. For instance, strain sensors can be printed onto the surface of structural elements to monitor their integrity during launch and space travel. As such, this real-time data can enhance the safety and reliability of missions while reducing weight by eliminating additional sensor housing and wiring.
Printed Antennas
As Communication is vital for space missions, antennas are essential components and printed electronics offer a lightweight alternative to conventional antennas. If antennas can be printed directly onto the payload structure, then there is no need for external bulky and heavy antennas. This not only reduces weight but also enhances communication efficiency, as the printed antennas can be designed to match the payload’s shape and minimize signal loss (especially if designed with AI).
Miniaturization and Multifunctionality
Printed electronics enable the miniaturization of components and the integration of multiple functions into a single printed element. This capability allows for the consolidation of various payload systems into a smaller footprint, reducing both weight and volume. For example, printed sensors can be integrated with printed circuitry, eliminating the need for separate sensor housings and interconnections.
What challenges do printed electronics face?
While printed electronics certainly introduce many potential advantages, there are still numerous challenges that prevent their widespread use, especially in the space industry.
By far, one of the biggest challenges faced by printed electronics is that they are still in their infancy, and complex components are rarely found in commercial use. Printing antennas, resistors, and capacitors is fairly simple, but complex components such as transistors and amplifiers require complex structures. Furthermore, active circuits designed using printed electronics are far larger than their semiconductor counterparts, meaning that only simple functions are generally available.
Another challenge faced by printed electronics is that some printed materials can be fragile. This means that they would likely see fractures during times of high g forces, thereby making them unsuitable for use in rockets. However, there are some printed materials that show a great deal of flexibility, meaning that they could likely survive take-off, but considering that many of these are based on hydrogels and/or polymers, phenomena such as outgassing could see these circuits breakdown in the vacuum of space.
However, advancements in the field of printed electronics are promising. According to the European Space Agency (ESA), they are exploring the use of printed electronics to enhance the robustness of space missions while reducing mass, manufacturing lead times, and cost1. The process involves 3D printing electrically active materials such as metals or carbon-doped polymers to form devices like transistors, capacitors, and resistors, along with the electrical connectors linking them together.
The Future of Printed Electronics in the Space Industry
Printed electronics have the advantage of flexibility, being able to be printed in virtually any shape, with flexible substrates laid down along complex geometries. They can also be produced at a much lower cost and done so locally, reducing the turnaround time from 3-4 months to 12 hours1. This aligns with the low-volume high-variety mix requirements of the space industry.
Moreover, 3D printing opens the prospect of in-situ repair and production of parts in locations such as the International Space Station, the Moon, or Mars. Printed electronics present a more sustainable approach in terms of production, with 65-80% less waste, less manufacturing tooling, and lower temperatures, with a far reduced carbon footprint1.
Overall, printed electronics show great promise across many industries, and it is very possible for printed electronics to find their way into the space industry. However, unless the many challenges facing printed electronics can be met, it is highly likely that they will not be dominating payloads heading to space any time soon.
Despite the challenges, printed electronics is not intended to compete with but rather complement the traditional silicon electronics industry. The most promising direction is actually 'Hybrid Printing', combining printed substrates and functional inks with traditional components to get the best of both worlds1. With continuous research and development, printed electronics could play a significant role in the future of space missions.
NASA's Jet Propulsion Laboratory, in collaboration with industry partners Xerox PARC and Boeing Research and Technology, is also exploring the potential of printable spacecraft. The concept involves using printed electronics to design and fabricate an entire functional spacecraft, from the scientific sensor to the data downlink, capable of surviving and functioning in a space environment2.
In another development, Space Foundry and Iowa State University, supported by NASA’s Flight Opportunities and Small Business Innovation Research (SBIR) programs, have been advancing methods for 3D printing of electronics in microgravity. This technology could enable the manufacturing of sensors, circuits, and other electronics in space, which is crucial as NASA prepares to send astronauts back to the Moon3.
Case Study: The Use of Printed Electronics in the Mars Rover Mission. The Mars Rover mission, launched by NASA, utilized printed electronics in several key components of the rover. This included the use of printed sensors to monitor environmental conditions on Mars and printed antennas for communication with Earth. The success of these components in the harsh conditions of Mars serves as a testament to the potential of printed electronics in space missions6.
The Role of Solution-Based Printing in Space
Space Foundry's process leverages a single-step approach that doesn’t require heat or ultraviolet curing, which could lessen the impact on astronauts’ time, lower costs, and improve the versatility of printing electronics for a wide range of applications. They have successfully printed silver electrodes and a Wi-Fi antenna during microgravity flights and have also developed a proprietary ink for printing copper electrodes3.
Iowa State University's system for electrohydrodynamic inkjet printing addresses the challenge of the lack of gravity needed to drive the flow of liquid inks in space. The system leverages electrical force to drive ink flow, replacing the need for gravity. They have successfully printed microelectronics, including a humidity sensor, during microgravity flights3.
A comprehensive review of the applicability and application of solution-based printing for manufacturing electronics and sensors in space has been presented. Solution-based printing (SP) in space can be considered a disruptive technology for in situ manufacturing and maintenance of functional devices during the long duration and endurance of space exploration and crewed spaceflight. The potential space applications of SP techniques include flexible solar cells, soft and wearable sensors, and space-based antennas. The survivability of printed electronics in space is also analyzed4.
The Use of Solution-Based Printing in the International Space Station. Astronauts aboard the International Space Station have used solution-based printing to manufacture replacement parts and tools, demonstrating the potential of this technology for in-situ manufacturing in space.
Liquid Metal Printed Electronics: A New Frontier
Another emerging technology in the field of electronics manufacturing is liquid metal printed electronics (LMPE). Compared to conventional electronic manufacturing, LMPE offers many extraordinary opportunities, such as large-area printing, pervasive adaptability, flexibility for personal use, low cost, high performance, and environmental friendliness. More uniquely, liquid metal printing allows customised electronic products on demand to fabricate electronics spanning from 2D plane surface to 3D structure and on any desired substrates. This deems it to reshape modern electronics towards a more user-friendly and sustainable future5.
Emerging Applications: Liquid Metal Printed Electronics in Satellite Design. Several satellite manufacturers are exploring the use of liquid metal printed electronics in their designs. This technology allows for the creation of flexible, lightweight electronic components that can be easily integrated into the satellite structure, potentially leading to significant weight and cost savings.
A snapshot into the swiftly evolving field of liquid metal printed electronics5.
In conclusion
The potential of printed electronics in the space industry is vast and exciting. While the technology is still in its infancy and faces significant challenges, ongoing research and development are paving the way for its wider application. The ability to create lightweight, flexible, and customizable electronic components could revolutionize the design and functionality of payloads, potentially leading to significant cost savings and improved mission outcomes. As we continue to explore the final frontier, the integration of printed electronics may well become a key factor in the success of future space missions. The journey of printed electronics is just beginning, and its impact on the space industry could be as boundless as space itself.
References
1. European Space Agency. (2023). Printing electronics to help space missions lose weight. Retrieved from https://www.esa.int/Enabling_Support/Space_Engineering_Technology/Printing_electronics_to_help_space_missions_lose_weight
2. NASA. (2012). Printable Spacecraft: Flexible Electronic Platforms for NASA Missions. Retrieved from https://www.nasa.gov/directorates/spacetech/niac/2012_Phase_II_printable_spacecraft/
3. NASA. (2022). Microgravity Testing Advances Space-Based Printing of Electronics. Retrieved from https://www.nasa.gov/centers/armstrong/features/microgravity-testing-advances.html
4. Wang, Q., Zhu, Z., & Zhu, Y. (2022). Solution Printing of Electronics and Sensors in Space. Advanced Engineering Materials. Retrieved from https://onlinelibrary.wiley.com/doi/abs/10.1002/adem.202200173
5. Zhang, J., Yao, Y., Sheng, L., & Liu, J. (2021). Pervasive Liquid Metal Printed Electronics. Advanced Science, 8(3), 2003630. Retrieved from https://www.ncbi.nlm.nih.gov/pmc/articles/PMC7814192/
6. Peter Zelinski Editor-in-Chief, Additive Manufacturing (2021). 3D Printed Parts on the Mars Perseverance Rover: The Cool Parts Show #23. Additive Manufacturing, Retrieved from https://www.additivemanufacturing.media/articles/3d-printed-parts-on-the-mars-perseverance-rover-the-cool-parts-show-23
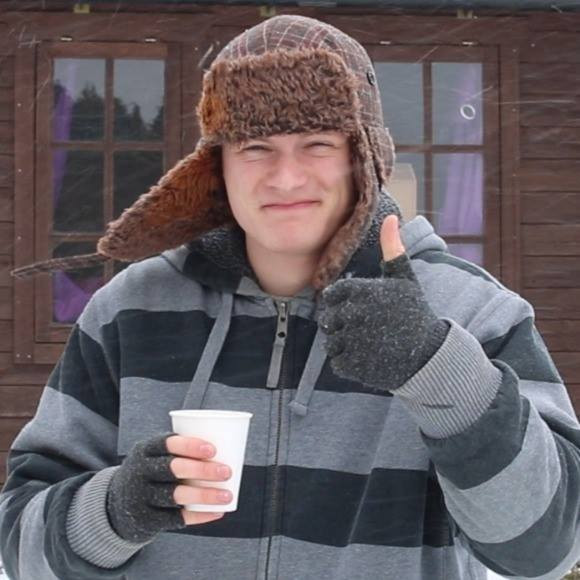