Bringing Custom Chips to the Masses: The Story of Tiny Tapeout
Insights | 13-03-2023 | By Robin Mitchell
The Tiny Tapeout project, which provides an opportunity for individuals to create custom semiconductor chips, is preparing for its third wave of chip fabrication, Tapeout 3. With 198 slots already filled up, only 49 slots are left for those interested in designing their own ASIC, FPGA, or CPLD device, with the chance to have it fabricated on silicon through the tapeout process. This project offers a unique opportunity to learn about integrated circuit design and transistor-level circuitry, as well as J-Tag programming and tapeout procedures. What challenges does the world of semiconductor fabrication face, what is Tiny Tapeout, and could the future of semiconductors see low-end chip production for individuals?
What challenges does the world of semiconductor fabrication face?
While no one can doubt the importance of resistors, capacitors, inductors, and transistors, the integrated circuit is by far the single most important development in the field of electronics. The ability to integrate billions of components onto tiny dies enables electronic devices to perform countless calculations and execute complex applications, all while measuring just a few mm across and consuming a few watts at most (of course, desktop and server CPUs can easily consume hundreds of watts, but for the most part, everyday integrated circuits consume very little power).
Traditionally, semiconductor devices have been designed and manufactured specifically by semiconductor foundries due to the extreme complexity involved. For example, Texas Instruments have developed its own range of semiconductor products that pair well with their in-house foundry services, and this has been the case for decades. Intel is another example of a company that designs and manufactures its own semiconductors.
However, not every electronic design can use off-the-shelf components, and there are many applications where having a customised semiconductor can be massively beneficial. For example, those designing high-speed digital systems may require unique bus interfaces or fast analogue capturing devices that simply don’t exist on the market. Another example, albeit an ancient one, was when many computer manufacturers in the 80s required custom chips that could share memory with mainstream processors (such as the Z80 and 6502) for the sake of video generation, keyboard scanning, and peripheral interfacing.
As such, many semiconductor foundries have opened their doors to third parties who have the design but not the manufacturing capabilities, often referred to as fabless business (Xilinx is a famous example). Customers can submit their own chip designs, and foundries can tape them out into custom packages specifically targeted at one application (called Application Specific Integrated Circuit, or ASIC for short).
But as great as ASICs are, they are costly to set up due to the need for high-end tooling and the fact that ASICs cannot be purchased individually. Because it is not uncommon for initial production runs for low-end ASICs to well exceed $10,000, only large businesses tend to benefit from ASIC services, such as Apple and Microsoft.
Thus, smaller businesses and individuals are yet to experience the advantages of custom semiconductorxs, which will unlikely change in the near future unless a company can develop a low-cost production run for simpler semiconductors.
What is Tiny Tapeout?
For those looking to create their own semiconductor, Tiny Tapeout offers a potential solution that is guaranteed to those who join and pay. Simply put, Tiny Tapeout is an education project that combines hundreds of individual designs into a single chip, and that chip is then produced at quantity to not only guarantee working parts but to also reduce the cost of each chip.
Instead of giving each designer their own custom chip with their own design only, all designs submitted to the production run are combined into a single chip package, and these designs are daisy-chained together, similarly to J-Tag. Using external I/O controls, the design to be used is selected, and the I/O ports to that design are routed to the chip’s physical pins. That way, every member of the production run gets a chip with everyone’s design and can select the design (including their own) that they want to activate.
By using this method, Tiny Tapeout only has to create one die design which is repeated across an entire wafer, and the use of daisy-chained I/O allows for the whole design to be easily tested and verified for functionality. In addition to a custom chip, Tiny Tapeout also offers a PCB with the chip pre-soldered onto a PCB with selector switches and input/output pins. This helps individuals test their designs as well as integrate their custom ASIC into projects.
Recently, Tiny Tapeout announced its third production run, which still has 49 design slots available (with 198 already being used). Unlike other services that use a lottery system, Tiny Tapeout is guaranteed so long as users pay a fee upfront, with the entire PCB and ASIC costing $100 per board. Tiny Tapeout also provides a host of tools that enable users to design and compile their design for free, reducing the cost burden on those looking to create their own semiconductor circuits.
Could the future see low-cost custom semiconductors for individuals?
While microcontrollers, FPGAs, and CPLDs offer engineers the ability to integrate custom functionality into semiconductors, it has been a long dream to get custom semiconductors at a price comparable to custom PCBs. Of course, the high-end technologies needed to manufacture modern semiconductors makes such a dream a technical impossibility.
However, the technology needed to manufacture semiconductors from several decades ago (the late 1980s to early 2000s) is far more accessible. As such, it may not be long before smaller foundries pop up with the sole purpose of manufacturing custom semiconductors using older technologies. While such devices may not have strong commercial opportunities, the ability to create custom ICs could prove beneficial to those in education, as well as those needing to find replacement parts for obsolete components.
Tiny Tapeout utilises low-cost ASIC solutions and group funding to reduce the cost of each chip manufactured, but the need to share a large portion of die space with other designs limits what can be done using Tiny Tapeout. At the same time, having 1000 custom chips can be far too many for most individuals, making Tiny Tapeout an extremely cost-effective solution.
So, if you are looking to create your own semiconductor ASIC and don’t mind sharing space with others, consider grabbing one of the last slots available for Tiny Tapeout 3!
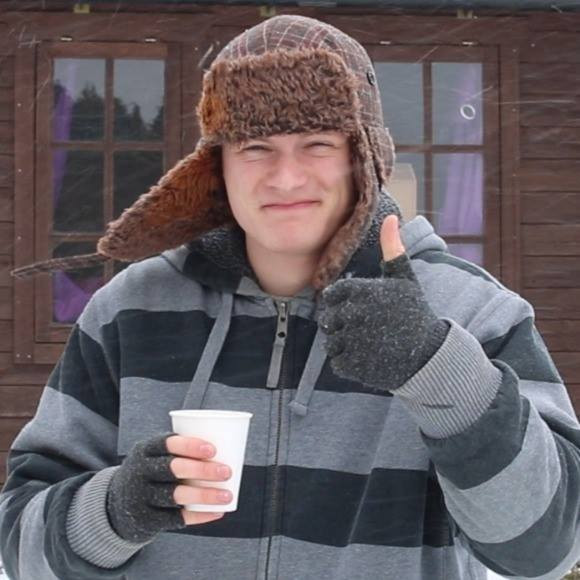