Hyundai To Manufacture Their Own Automotive Semiconductors
Semiconductors | 08-08-2022 | By Robin Mitchell
Recognising the challenges faced by the semiconductor industry, Hyundai recently announced that it will be manufacturing its own automotive semiconductors to help secure its own supply chain as it moves into the electric vehicle industry. Why are EVs particularly affected by the semiconductor shortage, what will Hyundai be doing, and could other manufacturers also start developing their own silicon?
Why are EVs particularly affected by the semiconductor shortage?
The semiconductor shortage caused by the COVID pandemic of 2020 has left no industry unscathed, and this fact has made the world realise the importance of semiconductors in general. Worse, the supply chain issues faced by semiconductors have also taught the world how the vast majority of next-generation semiconductors are manufactured in Southeast Asia, which has led to numerous national security concerns.
While most industries have been affected by the semiconductor shortages, the automotive sector has particularly been affected due to the sudden resurgence of car manufacturing and the inability of semiconductor foundries to tape out automotive-grade parts in a timely manner. In fact, the situation has become so dire that one company was reported to have purchased new washing machines just to extract key parts for their own products (while it was never confirmed to be an automotive company, we suspect that it was due to the similar environments faced).
Modern cars are said to be so integrated with electronics that they are considered to be more computer than vehicles. But EVs are even more integrated with an estimated 500 to 1000 semiconductors per vehicle (approximately three times the number of combustion engine-based vehicles). As such, it is no surprise that EVs are particularly vulnerable to semiconductor shortages.
Their extensive use of electronics stems from their electric nature; they require batteries that need charging circuits, battery cooling is provided with electric fans, all pumps are motor based, and the increased use of modern features such as collision detection and enhanced cruise control all requires intensive computational processing. As such, EVs are highly dependent on market fluctuations in electronic components that go beyond semiconductors.
Hyundai announces intention to manufacture its own chips
Recognising the numerous challenges faced by semiconductor suppliers, Hyundai recently announced that it will manufacture its own automotive-grade semiconductors. To manufacture the part, Hyundai will be turning to its semiconductor affiliate Hyundai Mobis which will focus on developing and producing power semiconductors.
The large voltages and currents involved with EV batteries mean that high-power semiconductors are required, and maximising efficiency in such devices helps extend an EV's range. Considering that over 90% of the world's automotive semiconductors are manufactured by just six companies (including Renesas, Microchip, and NXP), the move by Hyundai would help to move manufacturing to South Korean companies, which not only supports local supply chains but also reduces the dependence on South Korean auto-makers on foreign suppliers.
Hyundai also noted that while power semiconductors were a primary focus, it is also looking into developing platforms capable of accelerating AI. The increasingly complex nature of vehicles and the use of embedded AI require advanced semiconductors, but the disruption to the semiconductor supply chain makes it challenging for businesses to develop such technologies.
Could more businesses manufacture their own silicon?
Over the past few years, more businesses have been moving towards custom silicon due to the numerous advantages they provide. For example, products designed to be portable need to make the most of every watt of energy consumed, and this is difficult to do when using off-the-shelf components (as these parts will undoubtedly have internal components and peripherals not needed by the end design). Additionally, engineers can focus on adding additional peripherals suitable for their end design, which means that custom silicon devices are not only highly efficient but also highly capable.
An excellent example of such a device is the Apple M1 SoM. To start, it uses custom-designed ARM cores that offer low-energy capabilities and high-performance processing (split into two different core variations). Secondly, the M1 takes advantage of neural network accelerators to improve the speed of AI tasks while minimising energy. Thirdly, system RAM is moved into the module itself (as opposed to being external), and this helps to improve performance. The end result of the M1 is a chip that can be used in a desktop machine, a laptop, or a tablet and provide efficient computing for each scenario.
But in the case of Hyundai, not only is custom silicon being explored but so is in-house manufacturing. Many industries (including the automotive sector) are not reliant on the latest semiconductor technologies and are quite happy to use semiconductor nodes from 2000. Considering that manufacturing such devices has become relatively easier, it is becoming more economical for large businesses to fabricate their own devices.
As such, we may start to see large businesses establishing their own private foundries that solely focus on company products.
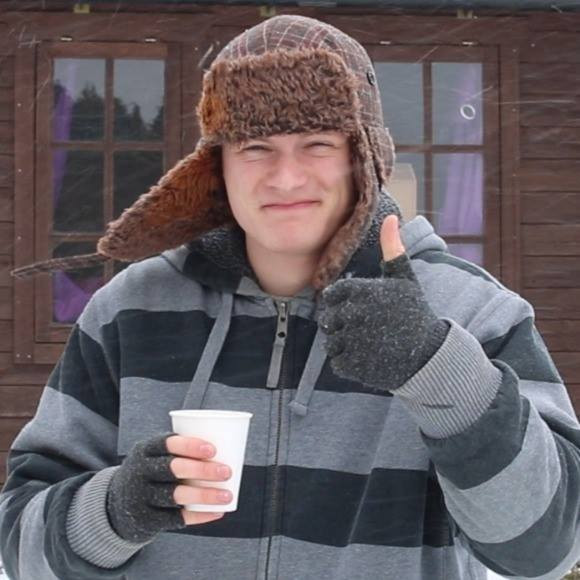