Mitsubishi Ultra-thin Precision Position Detectors
| 14-07-2020 | By Robin Mitchell
This month, Mitsubishi will launch a marketing campaign for its latest precision position detectors. What makes this precision detector different from others, and how can it benefit those in automation?
Linear Motion Positioning
Precision positioning systems are incredibly important in industrial processes, whether it be an automation step, or for use in precise machining. In rotational systems such as motors, positioning is rather easy to accomplish using a wide range of different techniques. For example, rotary encoders can provide the absolute angle of a shaft, and rotary encoders come in a variety of different types. Linear systems that are driven by a motor can achieve precision positioning with the use of a rotary encoder on the motor, and homing switches to provide references. Linear systems can also achieve positioning with the use of a laser, but these cannot offer precision positioning over short distances in the um range. Another method for positioning would be the use of patterns on the linear rail, but again this would have a low resolution.
Mitsubishi Heavy Industry’s ultra-precision position detectors
To provide a solution for linear systems that require a precision position sensor Mitsubishi Heavy Industry have announced their latest marketing campaign to promote the MPFA Series. The new position detectors utilise technology found in Mitsubishi’s MP Scale, which is found generally in machine tools. Unlike other position detectors, the new system operates like a tape measure whereby the main sensor body is mounted to the end of a rail, while the end of the tape is connected to the moving platform. As the platform moves away from the sensor body, the coiled tape unwinds, and the sensor provides a position based on how much tape has been pulled out. This method offers linear systems with the highest speeds and precision currently possible with such systems.
Credit: Mitsubishi Heavy Industries
The MPFA series provide a resolution of 0.1 um, and a response speed of 30M per second. Previous scale units measured 10mm in thickness, but the new MPFA has a diameter of only 0.4mm. This is only possible thanks to the tape design, and the result of the reduced size allows for it to be directly mounted into linear motor stages. The use of a non-contact structure also eliminates precision deterioration, something that occurs in the natural ageing of contact-based position systems. The combination of a non-contact measurement method and the MPFA precision allows them to be utilised in even the harshest environments involving precision machinery that generates dust, oil, and condensation.
The new linear position detectors also come with MP VIEW as standard. This software allows for a user to connect the sensor to a computer, and read different readings from the sensor, including its current position and the gap between the scale and head. The software makes it easy for engineers to make adjustments when installed as well as performing maintenance.
Conclusion
The MFPA series of ultra-precision position detectors demonstrate how age-old designs such as the tape measure can provide solutions to modern problems. Its high-speed capabilities of 30m/s, and the ability to measure down to 0.1um is an impressive feat of technology and a must in any linear application involving precision machining.
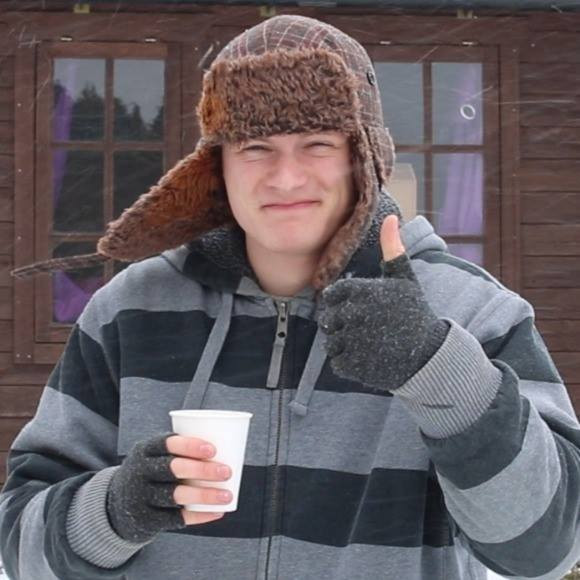