SiC and GaN Power Semiconductors Extend EV Driving Range
Insights | 22-05-2025 | By Gary Elinoff
A Silicon Carbide based EV Power Inverter: Wolfspeed
Key Takeaways about SiC and GaN Power Semiconductors Boost EV Driving Ranges:
- EVs rely on a DC-based power distribution system.
- The various subsystems within an EV require many different operating voltages, and drive motors typically require 3-phase AC.
- GaN and SiC power semiconductors operate at high speeds and can handle high voltages and power.
- GaN and SiC are both wide bandgap semiconductors, and the power semiconductors that they are used to produce feature similar properties. There are also significant differences that designers can use to their advantage.
Introduction
It’s been said that a modern automobile is essentially a computer on wheels, with all the sensors, cameras, computers and other essential electronics that communicate with each other on a never-ending moment-by-moment basis. Electric vehicles (EVs) take it a step further. They eschew gas tanks and fuel systems with their bedlams of lines and hoses. They also have no need for catalytic converters and pollution control systems that seem to take up half the space under the hood.
Instead, the fuel tank is replaced by a Lithium Ion Battery (LiB) that holds perhaps 200 kilowatt hours of electric power. This battery operates at 400 Volt DC (VDC), with newer systems sporting 800 volt potentials.
The only problem is that the various systems and components of an EV operate at many different voltage levels. And some, like the powerful electric motor that makes the car go, actually require high power AC.
So an EV, in addition to being a computer on wheels, is also a traveling power conversion and power grid on wheels. And, as we’ll see, the efficient performance of an EV’s DC-based power distribution system depends on the performance of wide bandgap semiconductors (WBG), specifically gallium nitride (GaN) and silicon carbide (SiC).
But first, some historical background.
Thomas Edison Gets the Last Laugh on Tesla
So what’s that got to do with power transistors based on GaN and Sic and their tie-in to electric vehicles? Plenty!
The greatest inventor of all time, Edison, envisioned a DC grid to power his marvellous new electric light bulbs, starting in Lower Manhattan. Tesla, the father of electrical engineering, pointed out there was no practical way to switch the high voltages best for transporting power over distances down to the lower voltages most suited for home and office. Even with 1880’s technology, changing higher AC voltages down to lower AC voltage was easy enough through the use of transformers.
Ultimately, Tesla’s partisans won the fight, and AC became the worldwide standard. However, power semiconductors based on GaN and SiC may have turned that decision on its heels because grids based on DC, at least within the confines of EVs (electric vehicles), are the standard way to go.
Edison is vindicated 140 years later, and here’s why.
What Power Semiconductors Do
One of the things they do, relevant to our purpose here, is that they can turn ON and then turn OFF fast. Really, really fast. If they are fed by DC voltage, when they are turned ON, A DC voltage is output, when the power semiconductor is turned OFF, the output returns to zero. The image below is an idealized version of the result, and the waveform is described as pulsating DC.
Pulsating DC. Image source: Electropages
If pulsating DC is presented to the primary of a transformer, the transformer reacts in a similar manner had it been animated by AC in that the transformer’s output is an AC voltage. The voltage level of the resultant AC is governed by the turn ratio of the device’s primary to its secondary windings. So, DC can be easily changed into AC power at any voltage level.
Through similar techniques also based on WGB semiconductors, that AC can be converted to DC at any desired voltage level. Two points:
- To convert DC voltage at one level to DC of another potential, it is first converted to DC
- As we’ll see, these conversions can only be done efficiently with WBG power semiconductors.
So, what we have begun to discuss is a DC bus that can be used to originate multiple DC voltage levels, but over a century too late for Edison!
What is meant by “Wide Bangaps”?
GaN and SiC are what’s called wide bandgap semiconductors. As described by Infineon[1], “Wide bandgap, (WBG), semiconductors differ significantly from conventional semiconductors since they have a larger bandgap. A bandgap refers to the energy difference in semiconductors between the top of the valence band and the bottom of the conduction band. The larger distance allows wide bandgap semiconductor power devices to operate at higher voltages, temperatures, and frequencies.”
Bandgaps. Image source: Toshiba
In power conversion, WGBs are essentially being employed as super-fast switches; ON and OFF. Any internal resistance in a WBG switch, just as is the case in a mechanical switch, will cause a waste of power. This is because power, in this case wasted power, is equal square of current times resistance (P = I2R).
WBGs have much less internal resistance than Silicon (SI) power transistors, so by nature, they are more efficient.
Now, let’s look at the other advantages afforded by WGBs.
Higher Operating Temperatures and Smaller Size
Because WGBs can operate at higher temperatures without breaking down, there is less need for expensive, bulky heat sinks. SiC, for example, can operate at temperatures as high as 700℃, compared to only 150℃ for silicon (Si).
Additionally, WGBs pack more performance into a smaller size. This, and the temperature advantage, means that units based on WGBs can be more compact than Si-based counterparts.
Higher Power, Voltage and Frequency
This classic diagram illustrates and compares the properties of GaN and SiC power transistors.
GaN vs SiC. Image source: Infineon
What’s readily obvious is that GaN can be triggered ON and OFF faster than SiC. But, on the other hand SiC can handle more power, and actually more voltage, too.
Why is Faster Triggering important?
As described earlier, when presented to a transformer’s primary, pulsating DC creates an AC voltage in the secondary, and because WBG transistors can turn ON and OFF faster, the AC appearing in the secondary is of a proportionally higher frequency.
The key here is that transformers designed for higher frequencies are smaller and lighter. Since transformers and other magnetic components make up the bulk of the weight and size of most power supplies and converters, those based on high frequency WBGs will be smaller and lighter. These are critical values for EVs, because less weight translates into more miles traveled between charge ups. Additionally, any bit of physical space not taken up by power converters is available for other vehicular systems to enhance the customer’s safety and convenience.
In this arena, GaN has the edge because it can switch faster than SiC can.
Power and Voltage
As it stands now, most EVs sport either a 400 VDC or an 800 VDC system. Commercially available GaN transistors can handle 650 VDC at most. These GaN can operate in a 400 VDC world with a good safety margin but would be overmatched in an 800 VDC environment.
However, it isn’t either or. The SiCs can be employed in high-voltage spaces, with GaN being adequate for lower voltage. This is a tactic employed by some EV manufacturers.
It should also be noted that GaN is cheaper to manufacture because it can employ existing mature manufacturing infrastructure. As noted by EPC[2], “By growing a GaN epi layer on top of silicon, the existing silicon manufacturing infrastructure can be used, eliminating the need for costly specialized production sites and leveraging readily available large diameter silicon wafers at low cost.”
Traction Inverters
A traction inverter’s job is to convert the LiB’s High DC voltage into 3-phase AC for the EV’s drive motor, as illustrated below.
Functional diagram of a traction inverter and motor. Image source: Tektronix
Each of the three pairs of two WBG transistors generate one of the three phases of the overall AC power. The control unit makes sure that the 3 phases are generated at 120° with respect to each other. The AC powers the motor, which moves the vehicle.
When a gas or diesel vehicle is slowed down or stopped, it does so with a brake. This classical mechanical device applies friction to the spinning wheel, slowing or halting it, but the forward momentum of the vehicle is simply turned into waste heat. Not so with an inverter.
WBG-based inverters can also be employed to convert the vehicle’s forward momentum from heat to electricity. That electricity, you guessed it, is delivered right back into the battery. This is why EVs are so efficient at using and not wasting power. It’s also why the life of an EV isn’t cut short by all the parasitic heat generated by stop-and-go big-city traffic.
Wrapping Up
GaN and SiC power transistors, due to their fast switching speeds and high power handling capabilities, make EV power grids based on DC rather than AC not only possible but also highly efficient and flexible.
Power converters based on these WBG semiconductors are used to create ultra-fast DC pulses that are directly transformed into AC of correspondingly high frequency. The physical size and weight of transformers and other inductive components are inversely proportional to the frequencies they handle, so deploying WBGs in EVs saves size and weight, with a corresponding increased driving range due to power savings.
At the time of this writing, automakers are rapidly transitioning to 800 VDC LiBs, so the use of more expensive, slower switching SiC will be necessary in some applications, but not all. The first conversion from the 800 VDC battery will likely be SiC, and so will the traction inverter, which converts 800 VDC to 3-phase AC for the main motor.
However, now that more efficient GaN can handle increasingly high power and voltage, they are supplanting SiC in many EV use cases.
Challenges and Opportunities
For WBG semiconductors, the challenges are obvious. There needs to be more research into SiC to cut costs and to switch faster. Similarly, given the advantages of GaN, research must be continued into raising maximum operating voltages.
Since a given amount of power is equal to voltage times current (P = V*I), going from 400 VDC to 800 VDC means that although the voltage is doubled, the current required to deliver a given amount of power is cut in half. Let’s assume that any copper power line in an EV has a certain fixed resistance, R, and the power lost on that line, by formula, is I2R. If the current required at 400 VDC is I, the current required at 800 VDC is I/2. Power wasted in the line goes from I2R to (I/2)2*R, representing 75% less power wasted.
Less power wasted means more miles between charges, so, it’s a safe bet that the EV industry will in all likelihood move to an 800 VDC standard, challenging SiC to get cheaper and faster, and for GaN to achieve a higher breakdown voltage.
References
- Wide Bandgap Semiconductors (SiC/GaN). Infineon
- What is GaN? Gallium Nitride (GaN) Semiconductors Explained. EPC
Glossary of Terms
- WBG. The large energy bandgap between the valence band and the conduction band of these materials enables semiconductors to be constructed, offering superior speed, higher voltage, and higher power capacities.
- GaN (gallium nitride) and SiC (silicon carbide). These WBG materials are the basis of many power transistors that are in use today. GaN is faster, while SiC can work with higher voltages and power.
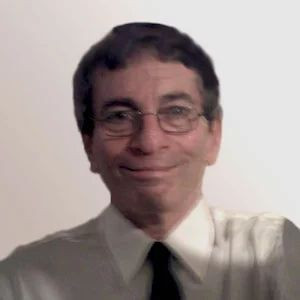