Cellulose Emerges as a Key Player in Sustainable Tech
Insights | 15-01-2024 | By Robin Mitchell
As concerns for sustainability in the electronics industry continue to increase, researchers are trying to find new materials which can help reduce our dependency on oil and toxic chemicals used in the manufacturing process of components. Now, researchers from Italy have potentially identified cellulose as a potential replacement material for future flexible electronics, allowing for electronics to be manufactured using sustainable sources. What challenges do current electronics face with regards to sustainability, what did the researchers discover about Cellulose, and could future electronics rely on organically sourced materials?
What challenges do current electronics face regarding sustainability?
Over the past two decades, concerns for the environment and climate have skyrocketed in light of increasingly devastating weather patterns, rising costs of raw materials, and the supposed scarcity of some minerals. Such concerns have pushed governments around the world to start introducing legislation regulating emissions, encouraging the development of renewable energy sources, and even outright banning certain products, such as single-use plastic cutlery.
This drive for environmental protection and reduction of non-renewable energy and mineral sources has also seen some changes in the electronics industry. For example, researchers are exploring the use of printed electronics utilising easily sourced materials such as graphite, paper, and organic semiconductors.
By using such materials, it becomes possible to create electronic devices that are not only sustainable in the long run but can also be easily recycled thanks to their biodegradability. However, creating such electronic devices is no small feat, and there are numerous hurdles that engineers have to face when incorporating such technology.
The first challenge that engineers need to overcome is creating reliable components that can survive for extended periods of use. Generally speaking, printed and thin-film electronics made from sustainable materials either suffer from poor performance or are extremely fragile, making it difficult to use reliably.
The second challenge is getting such materials to survive standard manufacturing practices. For example, photolithography is commonly used to fabricate metal interconnects, and this process requires the underlying substrate to survive metal deposition, photoresist application, exposure, development, etching, and stripping, all of which involve strong acids and alkali solutions.
The third challenge involved with printed electronics is cost. One of the major benefits of traditional electronics is that the technology is extremely mature, with the manufacturing process for both components and devices being well-developed and highly efficient. The result of these factors is that typical electronic devices are very cost-effective, but as printed electronics are still in their infancy, they are far from being a practical option for everyday devices.
Researchers look towards cellulose as a future electronics material
Recognising the need to find sustainable and environmentally friendly materials for future electronic devices, a team of researchers from the National Research Council Institute for Microelectronics and Microsystems in Italy have recently published their findings on how cellulose could power electronics.
Exploring the practical applications of cellulose in electronics, researchers have identified its potential in creating more sustainable and environmentally friendly devices. Cellulose, being biodegradable and derived from abundant plant material, offers a significant reduction in the environmental footprint of electronic devices. This shift towards cellulose-based components aligns with global efforts to minimise reliance on non-renewable resources and reduce electronic waste, a growing concern in the digital age.
According to researchers, it is believed that cellulose, a material commonly found in the cell wall of plants, could be a viable candidate for replacing plastic in everyday electronic components. However, in order for cellulose to be suitable for thin-film electronics, it not only needs to be made extremely thin (nanometres), but also not fall apart and be able to survive numerous manufacturing processes.
The innovation in cellulose technology extends beyond its environmental benefits. The Italian research team's work highlights how cellulose derivatives can be engineered to meet the rigorous demands of electronic manufacturing. By manipulating the properties of ethyl cellulose and hydroxypropyl cellulose, they have created substrates that are not only eco-friendly but also compatible with existing manufacturing processes like photolithography. This compatibility is crucial for the practical adoption of cellulose in the electronics industry, ensuring a smoother transition from traditional materials to more sustainable alternatives.
Thus, the team set out to find derivatives of cellulose that could be used to support future electronic components and a specific blend of the two was found. The two compounds, ethyl cellulose and hydroxypropyl cellulose, were chosen due to their opposing qualities that, when combined, create a highly suitable material.
In the case of ethyl cellulose, it is extremely hydrophobic, meaning that it does not mix with water (forming beads that do not break the surface tension of the water), while hydroxypropyl cellulose is extremely hydrophilic, mixing with water as soon as it makes contact. Individually, these materials can be used as substrates but suffer from opposing issues, with the ethyl being chemically stable but brittle and the hydroxypropyl being flexible but unstable.
After experimentation, the team was able to find a suitable blend that not only provided a good trade-off between flexibility and stability but could also be used with photolithography to create metal contacts. The researchers demonstrated the abilities of the blend by creating strain sensors that could be used to measure the degree of deformation and also developed a capacitive humidity sensor.
Could the future of electronics rely on organically sourced materials?
When it comes to the field of sustainability, there is a very clear trend of researchers trying to utilise organic material such as paper, and this makes perfect sense when considering that paper allows for inks and other materials to be easily deposited while being flexible, cheap, and biodegradable. Of course, it’s not just paper that is being exploited by researchers, but all manner of organic compounds that can be turned into diodes, LEDs, transistors, and sensors.
The move towards organically sourced materials in electronics is not just a trend but a necessity in the face of environmental challenges. The use of cellulose and other organic materials in creating electronic components represents a paradigm shift in the industry. It's a step towards a future where electronic devices are not only high-performing but also environmentally responsible. This approach could potentially revolutionise the way we think about electronics, from their production to their end-of-life disposal, making the entire lifecycle of electronic devices more sustainable.
The other major advantage to using organically-sourced materials is that they often eliminate the need for highly toxic and dangerous chemicals which are harmful to both human health and the environment. Furthermore, the creation of these compounds can also be environmentally problematic, requiring numerous chemical processes and mining of materials.
Overall, the need for sustainability cannot go understated as the Earth only has so many resources, and unless asteroid mining becomes a viable commercial enterprise, researchers will have to turn to alternative methods to ensure that the next generation of people can have access to the same comforts as we do.
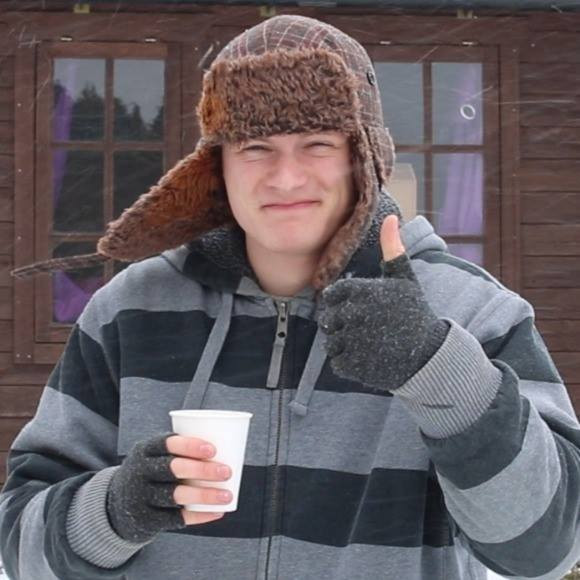