How Skin-like Sensors are Transforming the Field of Robotics
In The News | 28-07-2023 | By Robin Mitchell
Developing skin-like sensors for robots is the holy grail in robotics, but while countless sensing technologies exist, none are able to provide robotic systems with the same capabilities as that of human fingers. Now, researchers have developed a process that can provide robotic systems with a skin-like surface capable of arbitrary shapes and pressure detection. What challenges do sensors face in robotics, what did the researchers demonstrate, and why will such technologies be vital in future robotic systems?
The highly flexible sensor skin can easily adhere to various surfaces, including fingers.
What challenges do sensors face in robotics?
There is no doubt that robotic systems have the ability to control their position and strength far better than any human. The combination of micro-stepping and gear reduction allows for a robot to move individual joints by microns, while the use of large motors can provide enough force to lift a car.
And yet, despite this clear advantage, robotic systems struggle when moving from a delicate light object to something heavy. By contrast, a human can start lifting one hundred kilograms off the floor and then proceed to pick up a feather by its end, causing no damage whatsoever.
This ability to adapt in real-time to objects being picked is only possible thanks to the extreme sensitivity of human touch receptors and the high density of these receptors in human skin. On average, a human finger has around 3000 nerve endings, making them highly sensitive to small movements, vibrations, and changes in texture. In fact, it has been proven that the human finger is capable of detecting ridges in a material only 13nm in size, demonstrating the extreme sensitivity of the human finger.
Now, robotic systems can have touch sensors placed into grippers and joints, but unlike human fingers, no sensing solution on earth can provide a robot with the same degree of sensitivity (one or two sensors compared to 3000). This means that current sensing systems used by robots are crude, only providing minimal data on the object being held. Therefore, it is very difficult to get a solid gripper to lift a large, heavy object and then immediately lift a smaller, lighter object without prior knowledge of that object.
Researchers develop soft skin-like sensor for robots
The researchers, Sonja Groß and Diego Hidalgo presented their innovative work at the ICRA Robotics Conference in London. They developed a unique process where a conductive black paste is injected into liquid silicone. As the silicone hardens, the paste remains liquid, encapsulated within the silicone structure. This allows the sensor to detect changes in pressure as the silicone structure is deformed, thereby providing valuable data on the interaction with objects.1
The process is partially automated, with software building the structure for the sensor, which is then sent to a 3D printer for manufacturing. The sensors are versatile and can be attached to almost any object, making them particularly useful in robotics and prosthetics. When the sensors are pressed or stretched, their electrical resistance changes, providing information about the level of pressure or stretch. This principle is used to understand interactions with objects and to control an artificial hand that interacts with these objects.1
An image showcasing the sensor housing, versatile enough to be affixed to any form, including a dodecahedron. (Image courtesy of Andreas Heddergott / TUM).
Recognising the challenges faced by robotic systems, researchers have been trying to find soft materials to create advanced touch sensors for decades. While there have been some impressive discoveries and developments, none thus far have been able to provide robots with the same level of dexterity found in humans, and sensors that can provide dense sensing matrices often suffer from being ridged and difficult to work with. However, a recent development by the Munich Institute of Robotics and Machine Intelligence researchers may soon provide soft-touch sensors to future robotic systems.
To create their sensors, the researchers turned to printed electronics, as these have proven to work well with flexible materials. At the same time, the use of printable electronics also makes any future designs production friendly, thereby making it more likely to succeed in a commercial environment.
Sensor technology embedded in silicone, utilising conductive ink (Image courtesy of Andreas Heddergott / TUM).
The sensor itself consists of a conductive black paste that is injected into liquid silicone. During this process, the silicon hardens around the paste, but the paste remains a liquid. As such, any deformations on the silicon structure result in compressive forces acting on the internal liquid, and this changes the resistance of the sensor.
Furthermore, the researchers were able to demonstrate how their sensors could be printed directly onto flexible surfaces. In their initial findings, two different sensor types were mounted onto a single-finger glove; one strain sensor and one contact sensor. The researchers then used two sensors, one on a human finger and one on a robotic finger, to mirror the position of the human finger (such that the robotic finger would match the strain in the human finger).
Why will such technologies become vital in the future?
Currently, most robotic systems operate in controlled industrial environments behind numerous safety barriers, and while this is perfectly adequate for modern needs, robots that intend to interact with humans will need to be far more aware of their surroundings. Modern visual systems already allow robots to easily navigate, while audio systems can record conversations and listen out for unexpected noises.
However, unless a robot can be given a decent level of touch, it will never know how much force they are exerting on objects and people. A simple shaking of two hands between people could easily result in a broken hand if a robot is unable to detect the amount of pressure being applied. Sure, it is possible to estimate this via the amount of current being applied to motors, but this type of sensing can only go so far.
Adding touch sensors to robots not only allows them to control their strength but can be used for non-verbal communication and object recognition. For example, a robot moving into a dark area carrying a bag would be able to feel where exactly the object is and where best to hold it. This could also be useful should someone remove an item from a robot's hands, thereby signalling to the robot that the object is no longer there.
The potential applications of this technology are vast. For instance, in healthcare, robots equipped with these sensors could assist in delicate surgical procedures or in handling fragile medical equipment. In manufacturing, they could be used in assembly lines to handle delicate components without causing damage. In the home, they could enable more sophisticated and responsive domestic robots. As Sonja Groß, one of the researchers involved in the project, stated, "Our technology could revolutionise the field of robotics."1
What the researchers have developed is certainly exciting, and it won't be long before we start to see complex sensor matrices printed onto flexible substrates that can provide hundreds of contact sensors for robots.
References
- Groß, S., Hidalgo, D. (2023). "Robotik: Neue hautähnliche Sensoren passen fast immer". The Technical University of Munich. Available at: https://www.tum.de/aktuelles/alle-meldungen/pressemitteilungen/details/robotik-neue-hautaehnliche-sensoren-passen-fast-immer
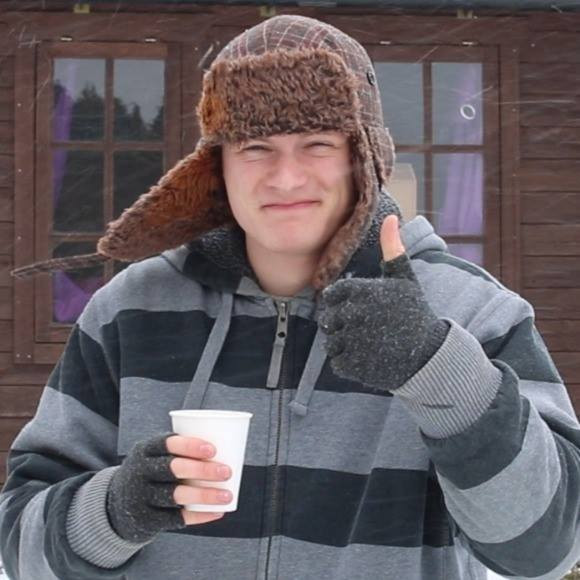