Samtec: Server-Grade Performance in Intelligent Edge Computing Applications
Insights | 02-06-2023 | By Robin Mitchell
In the ever-evolving world of technology, the demand for computational power is a constant. As engineers continue to push the boundaries of what's possible, the need for more robust and efficient systems becomes increasingly apparent. This is particularly true in the realm of embedded designs, where the challenges of increasing processor performance, power requirements, and connector capabilities are ever-present. Embedded designs refer to the process of integrating software and hardware in a specialised system to perform dedicated functions. In simpler terms, it's like the brain in your smartphone that allows it to perform all its unique functions.
This article delves into these challenges, exploring the solutions offered by industry leader Samtec and shedding light on the future of connectors in embedded designs. With a focus on the practical implications of these advancements, we aim to provide a comprehensive overview of the current landscape and the exciting developments on the horizon.
The challenges with embedded designs
If one fact has remained true since the development of the first computers, it is that the demand for computational power continues to increase. As new computing platforms are developed, engineers quickly find ways to not only maximise the capabilities of such systems but develop applications that require more resources, putting pressure on the computing industry to develop even better hardware.
However, as processor performance increases, so does the power requirement. This can clearly be seen when looking at the history of CPUs, with the first devices operating in the megahertz range with a few watts of power consumption and the latest devices operating in the gigahertz, where power consumption can easily reach 100W or more.
One area that has seen a dramatic rise in computational requirements is the automotive industry. Vehicles of the past would contain a number of simple electronic modules responsible for measuring fuel, controlling windows, and providing a comfortable internal cabin environment via AC, but this has changed with the advent of self-driving systems that require extremely powerful systems capable of analysing images and running machine learning algorithms all in real-time. If one fact has remained true since the development of the first computers, it is that the demand for computational power continues to increase. As new computing platforms are developed, engineers quickly find ways to not only maximise the capabilities of such systems but develop applications that require more resources, putting pressure on the computing industry to develop even better hardware1.
While this type of processing could be theoretically moved to a cloud environment, the lack of global coverage combined with numerous real-world realities means that no self-driving vehicle could ever take advantage of cloud computing, certainly not for real-time processing. As such, these embedded applications need to take the power of server-grade equipment and shrink it down into a system that can be made mobile.
But it’s not just automotive applications that can benefit from intelligent edge computing applications. There are countless industries now recognising the advantages of such systems. Renewable energy platforms such as wind turbines are integrating digital twins into each and every turbine so that engineers can better understand how each turbine behaves as well as predict potential issues before they manifest. In these applications, intelligent embedded systems can be locally installed to provide low-latency connections to sensors and other time-critical peripherals.
The trouble with shrinking connectors
Regardless of the application or design, a system can only operate as fast as its weakest link, and this is a common problem found in the field of computing. For example, even if a processor is capable of operating in the gigahertz, connecting RAM that can only operate in the hundreds of megahertz will instantly cap the performance capabilities of the processor. This is where Backplane / Micro Backplane connectors come into play. The same is true for external memory devices, networks, and peripheral ports being used.
In fact, the rapid development of processor technologies found in embedded designs is quickly outpacing the capabilities of connectors used in these applications, and this is putting pressure on engineers to find new solutions. For example, increasing data bandwidth is generally done by adding more data channels, but this will either increase the size of the connector or increase its density. If the density of the connector is increased, then pins are spaced much more closely, and this introduces a whole host of challenges, such as manufacturing tolerance.
At the same time, the increased power requirements of modern intelligent embedded computing applications also require connectors to be able to handle greater voltages and currents. By reducing the size of connectors, the power capabilities of each pin are reduced, meaning that increasing connector density doesn’t entirely help with the problem. This is where IDC & FFC connectors can be beneficial.
Design options for engineers
To try and solve these challenges, engineers have historically been able to rely on one of two main technologies: flyover cables and optical cables.
Flyover cables, as the name suggests, 'fly over' the circuit board, allowing signals to move directly from one point to another without having to navigate the circuitry of the board. This can significantly improve data transmission speed and reduce signal interference.
Optical cables, also known as fibre optic cables, use light to transmit data. This allows them to carry information at high speeds over long distances, and they're less susceptible to interference and signal loss compared to traditional copper cables.
Routing signals over PCBs using Twinax cable technology provide engineers with a very high-speed solution that can easily operate in the +100Gbps range over substantial distances. These cables can be used to connect two different areas of a PCB together or connect two different PCBs, but while they can travel far more than PCB traces, they are still limited to a few meters.
Optical cables provide engineers with a solution that is virtually immune to noise, provides a great deal of signal integrity, and can operate over extreme distances (well over hundreds of meters). These can be connected via Panel & I/O connectors. However, optical systems are generally expensive to implement and difficult to integrate, as electronic circuits require converters that can turn optical signals into electrical signals. This also increases the cost substantially, as unique connectors with integrated electronics are generally required.
How Samtec works to fix these challenges
Samtec has years of experience in interconnect and recognises engineers’ challenges in developing solutions for intelligent embedded systems. As such, Samtec has developed a range of solutions that can help engineers maximise the performance capabilities of complex computational platforms while simultaneously providing excellent power delivery and maximum flexibility in design.
New PICMG® COM-HPC® Interconnect Solutions utilise an industry format which provides access to a large number of I/O, provides greater memory capabilities, and supports higher powers compared to existing PICMG® COM Express® connectors. By encouraging engineers to develop compute modules that process data locally, these connectors can help engineers maintain performance in embedded designs, and the support for future standards can help to future-proof designs (such as PCIe 5.0, 100Gbps Ethernet, and USB 4.0).
Samtec COM-HPC® Interconnects from Samtec on Vimeo.
As FPGAs are also becoming increasingly popular in intelligent embedded designs, Samtec helped develop the VITA 57.1 FMC and VITA 57.4 FMC+ standards. These provide engineers with a standardised electromechanical interface providing I/O expansion for FPGAs and other related hardware. These connectors support up to 560 pins, making them highly applicable in I/O dense applications (such as real-time signal processing), and transceivers of up to 32Gbps are supported.
FPGAs, or Field-Programmable Gate Arrays, are unique types of computer chips that can be programmed after manufacturing to perform a wide range of tasks. They're like a blank canvas that engineers can configure to perform specific tasks, making them incredibly versatile in embedded designs.
For System on Modules in space-constrained applications, the Samtec AcceleRate® HD Ultra-Dense Mezzanine Strips offer engineers a high-density solution with a low profile. These connectors support up to 56Gbps PAM4, provide between 240 and 400 I/O connections, and have a 5mm width and stack height, which helps reduce the design size considerably. These connectors have been optimised for signal integrity and can also support PCIe Gen 5.0. For these reasons, the AMD Kira Adaptive SoMs have adopted the AcceleRate HD Ultra-Dense connectors.
Where are connectors headed in embedded designs?
Undoubtedly, as the complexity of applications increases, the need for greater processor performance will continue to grow, increasing the power, memory, and bandwidth requirements from such applications. At the same time, the use of reconfigurable hardware in the form of FPGAs will also increase as such hardware allows for future hardware updates without needing to replace physical components (this is especially important for upgrading hardware protocols).
When taking all of this into account, there is no doubt that the next generation of connectors will not only need to be able to handle these applications but also provide a degree of future-proofing. At the same time, connectors will have to continue to shrink in size to account for increased I/O requirements, but the increase in the density of connectors will introduce power constraints that the laws of physics will limit. Thus, future connectors in embedded systems will need to look for new methods to allow increased power capabilities, whether that is via additional power connectors or through new material sciences that support higher voltages and currents.
Finally, the increasing speed and bandwidth requirements from intelligent embedded designs will need to see server-grade performances, and this will make signal integrity “integral” to future designs.
References:
-
McKinsey & Company. (2020). Self-driving car technology: When will the robots hit the road? Retrieved from https://www.mckinsey.com/industries/automotive-and-assembly/our-insights/self-driving-car-technology-when-will-the-robots-hit-the-road" ↩
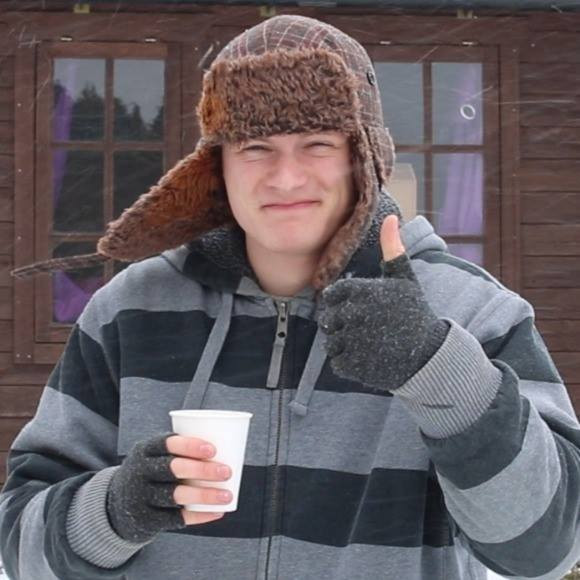