Another cause of the semiconductor shortage comes to light – Old technology
Semiconductors | 30-09-2021 | By Robin Mitchell
A recent report has brought to light another key reason for the automotive semiconductor shortage; old technology. How has this factor helped reduce automotive IC supplies, why can’t modern foundries help with this problem, and what challenges will the automotive industry face?
Why is old technology a factor in the automotive IC shortage?
The continuing shortage of integrated circuits shows no real signs of changing, and the automotive industry is feeling the full effects. Not only are new cars harder to find, but even used cars are increasing in value, making it a lucrative time to sell an older vehicle.
There is no doubt that the primary cause of the current semiconductor shortage comes from the COVID pandemic of 2020. Still, other factors continue to crop up that prevent the industry from recovering as fast as possible.
A new contributing factor has come to light and could signal the automotive industry to change how it develops new hardware. Simply put, the technology found in automotive-graded parts is generally at least one decade old, and modern semiconductors being produced are not being targeted towards automotive industries.
As it turns out, investors prefer to put their money into foundries at the forefront of semiconductor technology instead of those that use older technology, and this sees automotive-capable foundries in short supply. Therefore, no matter how much larger foundries such as TSMC and Intel want to help, they may be entirely incapable of producing automotive-grade parts.
Why are modern foundries struggling to help the automotive industry?
When the world was made aware of the severe semiconductor shortage, multiple foundries, including those at TSMC, announced that they would be prioritising automotive-grade parts. While this may seem like a good move, the truth is that these foundries often lack the capabilities to produce automotive-grade parts.
One would think that having access to the latest semiconductor technology would produce an integrated circuit conceived to date, but the truth is far from this. Circuit function and circuit capabilities are two very different things, with circuit function describing the electrical and logical behaviour of the circuit. In contrast, circuit capabilities describe the environmental factors of the circuit.
In the case of automotive electronics, the latest 5nm process would easily recreate any automotive processor on the market, describing the circuit function perfectly. However, the same 5nm process may not have the same environmental capabilities as older technology and could be more susceptible to shock, vibration, and temperature changes.
These differences in environmental capabilities between older and newer processes lead us to another challenge; reliability. It is well known that electronics in automotive environments need to be highly reliable, and components made using older processes have been heavily tested.
However, components made using the latest foundry process have not been tested anywhere near to the same degree, making their use in automotive applications dangerous. As such, modern foundries are unable to produce a large number of parts for the automotive industry.
What challenges will the automotive industry face?
The inability of many foundries to produce automotive-grade parts should be a sign to the automotive industry that it needs to update the technology used in vehicles. By doing so, automotive systems can take full advantage of modern technology, providing users with better experiences and vehicles with more capabilities. Furthermore, using the latest technology helps to encourage semiconductor foundries to peruse the latest technologies, thereby improving semiconductors overall.
However, it is very easy to say this when not dealing with the consequences of using modern technology. As Tesla has been experiencing the hard way, implementing new technologies into vehicles is incredibly risky and prone to real-life consequences such as lawsuits and product recalls. The use of any technology in an automotive application requires many millions of miles of testing.
To understand why this is the case, one can quickly calculate to appreciate just how many collective driving miles’ cars do daily. On average, each person in the UK drives 20 miles by car, and when multiplying this by the total population of the UK at 66 million, the total miles driven by vehicles each day in the UK is 1.3 billion miles. Of course, not every single person drives, and these figures are based on averages. However, even if the figure was inaccurate by two orders of magnitude, over 13 million miles would still be driven every day. If a new device fitted to every car had a failure rate of one in a million, there would be approximately 13 failures every day.
Trying to use the latest technologies in vehicles is a major challenge. The semiconductor industry needs to recognise that vehicles cannot simply use the latest technology or the newest foundries to pick up the slack in producing automotive parts. However, the industry cannot keep relying on old plants that lack investment and funds, as when these plants stop working, so does the automotive industry.
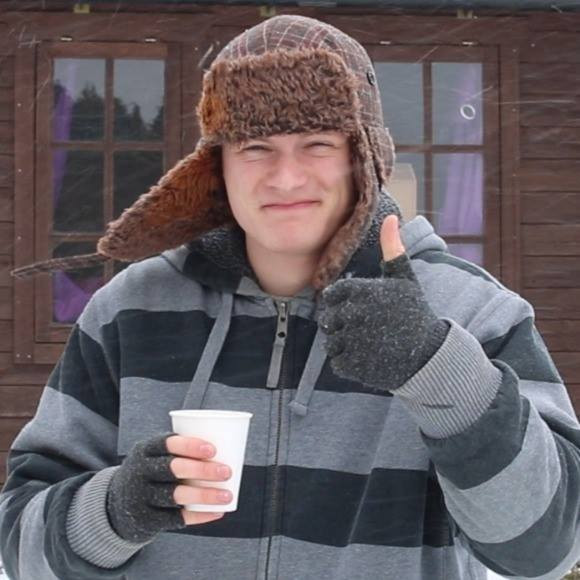