Machine Control of Industrial Laser Systems
| 29-01-2020 | By Nnamdi Anyadike
The increased adoption of automation technologies by industry, combining lasers and IoT, is a growing trend. Automation not only reduces costs but also increases flexibility and reliability by enabling material handling through remote sources. A key part of this involves integrated control solutions. These enable a wide variety of laser processes including laser cutting, laser welding, laser marking and drilling, and laser sintering.
Demand from industry is increasing for emerging applications like additive manufacturing, facial recognition, gesture recognition, LIDAR applications and IoT. And advanced lasers, especially those with 3D sensing capabilities, are enhancing interactions using technology. But now the race is on to develop ever more integrated control solutions. Recently, a number of companies have begun to collaborate in this area.
Siemens and SCANLAB cooperate on integrated control
At the end of last year Siemens AG the German technology group and SCANLAB GmbH the OEM manufacturer of scan solutions for positioning laser beams agreed to cooperate on the development of machine control for industrial laser systems. Advantages of integrated control include reducing cost overheads and shortening engineering time. “Laser machining is one of the growth areas in mechanical engineering in recent years. Through the merger of different providers, users benefit from a reduced integration effort and avoid unnecessary interfaces,” said the partners. The Siemens ‘Simatic IPC427E’ industrial PC is the platform for this new machine control system. SCANLAB’s scan system control card RTC6 is integrated into the hardware platform via APIs and connected directly to the Simatic S7-1500 software controller.
The Simatic IPC427E industrial PC with intelliscan head and integrated RTC6 control board, and Simatic S7-1500 software controller.
Credit: Scanlab
Precise Laser Manufacturing Group Launched
This year, 6D Laser LLC, an affiliate of ALIO Industries Inc, was officially launched with the stated mission of, “integrating ultrafast laser processing with precision multi-axis motion systems.” Key sub-system suppliers include Amplitude Laser, SCANLAB and ACS Motion Control. At the heart of 6-D Laser’s integrated ultrafast laser micromachining system is ALIO Industries’ Hybrid Hexapod. This takes a different approach to traditional 6 Degree of Freedom (6-DOF) positioning devices. “Rather than 6 independent legs (and 12 connection joints) ALIO’s approach combines a precision XY monolithic stage, tripod, and continuous rotation theta-Z axis to provide superior overall performance,” says the company.
The combination of serial and parallel kinematics in the hexapod provides orders-of-magnitude improvements in precision, path performance, speed, and stiffness. A feature of the hexapod is that it has less than 100 nm Point Precision repeatability in 3-dimensional space. In addition to ALIO, 6-D Laser is partnered with SCANLAB GmbH and ACS Motion Control, with which it has developed an unlimited field-of-view (UFOV) scanning solution. This is used for the coordination of motion control of the galvo scanner and positioning stages called XLSCAN. 6-D Laser is also partnered with ‘NextScanTechnology’ to provide high-throughput scanning systems.
Belgian University launches laser cutting control research
Last year, the Katholieke Universiteit Leuven (KU Leuven) called for applicants to take part in a research project that will develop advanced monitoring and control of laser cutting by means of high power fibre lasers. The project, which will target real time optimisation of processing conditions towards productivity maximization and quality control, is part of a larger, world class research group focussing on advanced manufacturing process development. “In recent years, fibre lasers have become the new standard for cutting different types of sheet metal materials,” said the university. Due to their high beam quality fibre lasers have hitherto been used in the fast processing of relatively thin sheets. However, more recent developments like beam shaping in combination with advanced optics have allowed for the expansion of applications to thicker grade materials. This has resulted in the need for improvements in process monitoring and control. The research will be conducted in close cooperation with a hardware solution developer.
CLAMIR facilitates advanced laser manufacturing processes
Control for Laser Additive Manufacturing with Infrared (CLAMIR), developed and commercialised by the Madrid based New Infrared Technologies (NIT), is an innovation that last year received an award from the European Commission. CLAMIR allows for the closed-loop feedback control of laser power. It uses a high-speed un-cooled infrared (IR) camera as a main sensor. This is coupled coaxially into the laser optics, allowing the camera to obtain IR images of the melt pool at a 1 kHz frame rate. The ability to install CLAMIR in an existing optical port makes it possible to be retrofitted into existing machines. The system consists of three main subsystems: the sensor; a high-speed IR camera sensitive in the 1–5 µm range; and un-cooled operation at room temperature. It also includes a software tool that configures the system for a chosen production machine.
Outlook
A recent report expects the industrial control and factory automation market to reach US$269.5 billion by 2024, from US$160.0 billion in 2018. This is equivalent to a CAGR of 9.08%. Growth can be attributed to the increased use of enabling technologies, including the rising adoption of industrial robots.
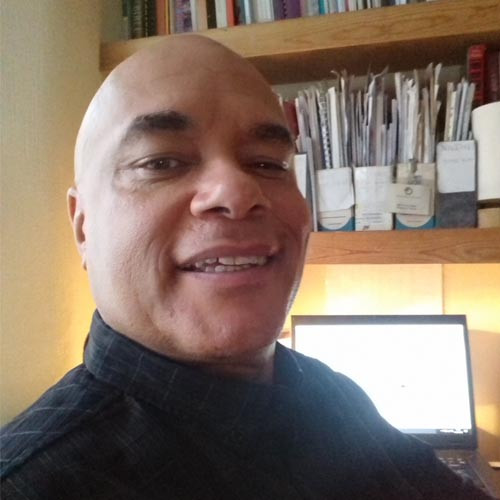