Cobots - Bridging the AI Gap for Industrial Automation
| 20-07-2018 | By Mark Patrick
There are two key issues, or challenges, currently facing industrial automation. Together, these challenges are driving the development of a new exciting form of robotics - the cobot. Depending on who you are talking to, a cobot may be defined as either a collaborative robot or a cooperative robot (with the former being the most common). While the precise phraseology is yet to be firmly settled, the meaning is more certain: A cobot is a robot that works closely together with humans, often in much the same way that two human workers would do so.
While much of the focus is on cobots for industrial use, the general concept is also applicable in healthcare, assisted living (for the elderly and disabled), office environments, etc. Early research at MIT suggests a collaborative team of humans and robots could reduce non-productive worker time by as much as 85%. Elsewhere, analyst firm Research & Markets has predicted that the value of the worldwide cobot business will to grow from $175 million in 2016 to $3.8 billion by 2021.
Cobots and flexible automation
The first of those two major challenges mentioned that the industrial automation sector has to tackle, and is thereby encouraging cobot development, is flexibility. This issue might be called the 'AI gap'. What this means is that artificial intelligence (AI) and machine learning techniques are rapidly becoming more capable within narrow domains - such as recognizing objects in any orientation or lighting environment - but broadening this narrow AI into a more flexible general intelligence is proving to be an uphill struggle.
There remains a huge divide between machine intelligence and human intelligence, and progress in bringing the two closer together is still very slow. A poignant example of this issue is human assembly line workers can quickly grasp how to integrate a new or redesigned component, but their robotic partners need extensive reprogramming and retooling to handle small changes. To put it bluntly: a simple or poorly-designed robot will continue to hammer square pegs into round holes forever - or at least until it runs out of pegs.
However, this ‘AI gap’ is in fact a major opportunity for cobots. Ideally, a cobot will perform the parts of a task that robots and production machinery are good at, while their human counterpart will take charge for the elements that require intelligence. To do this most efficiently though requires very close proximity between humans and large, complex machines - and that presents another challenge.
Cobots and safety
The second challenge slowing the advance of this new era of industrial automation is safety. While industrial robots have been working on production lines for decades, they are mostly isolated - being situated in cages or areas inaccessible to the human workforce. This is because these powerful and bulky machines can cause serious injury to a member of staff if they inadvertently collide with them (not to mention causing costly damage to themselves if they strike a forklift or some other piece of equipment).
Thanks to sensors, collaborative robots (cobots) are able to interact directly and safely with humans. By Daimler und benz Stiftung - Daimler und Benz Stiftung, CC BY-SA 3.0 de, Link
Historically, the first fatal injury directly attributed to a robot occurred at a Ford Motor Company plant in Michigan, back in 1975. Here a worker was crushed to death by a robot that failed to detect him when he unwisely entered the working area. Unlike two human employees working together, naturally understanding and anticipating each others’ actions and requirements, it is a significant engineering feat to design a useful industrial robot that can cooperate safely with a human in the same physical space, and this limitation obviously reduces efficiency.
Furthermore, safety regulations make it difficult to develop new cooperative processes on the factory floor, even when it might be feasible. Recently, international standards, such as ISO/TS 15066:2016 and ANSI/RIA R15.06-2012 have begun to delineate the specific requirements for safe operation of cobots. Some standards are addressing particularly difficult subjects, such as robots that are designed to come into physical contact with human users within the workspace.
Making cobots better
As we noted earlier, industrial robots are still very far from moving out of their narrow areas of expertise into more general purpose AI. But, nevertheless advances in AI, computing performance and sensor technology are making these automated machines more capable than they were in the past. In fact, the ability to work more closely with humans is a key area where progress is being made.
It is notable that innovations driven by the automotive industry's huge investment into self-driving vehicles have many useful applications in a cobot context. Safety is obviously the primary concern for autonomous vehicle developers, and the resulting safety-driven innovations in machine vision, LiDAR and other sensor/sensory processing technology are also very useful for making industrial automation less dangerous. For example, the challenge of an industrial robot arm detecting and avoiding an unpredictably moving human co-worker is, in general terms, quite similar to the challenge of an autonomous vehicle avoiding a collision with a jaywalking pedestrian.
Another field that, perhaps unexpectedly, has proffered up many useful contributions to cobot development is augmentation and assistance devices for the disabled. The same types of sensors and systems that allow a sophisticated artificial replacement limb to understand and carry out the intentions of its owner might be utilised by anyone to intuitively control a robotic arm, for example. Disabled assistance devices obviously have to work in very close contact with humans, and the decades of experience in making these devices safe can be helpful for industrial cobot developers. The touch-sensory and force-feedback technologies essential to a sophisticated artificial limb are very beneficial for cobots. They aid the development of intuitive features, such as the ability for a human to safely teach a robot arm a new task by hand guidance, in other words, by physically moving the arm through each stage of the job.
It takes very little imagination to realise that there are also useful synergies between augmented reality (AR) and cobot development. An AR headset can help a worker coordinate their actions better with a robot. We could say that AR allows humans to enter the cobots’ world, and perceive things as a robot does. The human can see what objects the cobot is aware of and be alerted to any objects that the machine has not noticed or has mis-identified - and this is in addition to the other benefits of AR in production and design. In summary, AR can make human interaction with cobots both safer and more efficient.
The hidden cobot bonus - scalability
Extrapolating the course of cobot development into the future reveals a surprising benefit of the cobot concept. In general, a production processes that uses cobots will be far easier to scale up, as well as being more flexible, than a production process based on traditional robots and automation.
The key reason for this is that if cobots are able to adapt to and cooperate with humans far more easily than old-fashioned robots can, then they should also be able to work better with other robots and cobots. A robot arm that can sense and avoid a human moving through its space, and work around them, will be equally capable of avoiding another robot. So, in the factories of the future, cobot could be added into the production line to perform a new task or to scale up production, with far less disruption than traditional retooling processes entail.
Read More: Academia, defence and business jump starting nanoelectronics
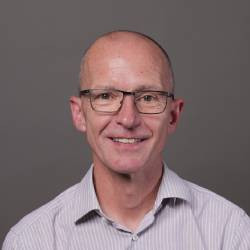