How EU Manufacturers Can Adapt to Trump’s Trade Tariffs
Insights | 27-05-2025 | By Jack Pollard
By Puneet Saxena, Corporate Vice President, Manufacturing Industry Strategy, Blue Yonder.
As of late April 2025, the global semiconductor industry, along with its associated supply chain and customer base, was still waiting for a tariffs announcement by the Trump administration. Just a couple of weeks earlier, Reuters were among a host of news outlets reporting that “Tariffs on imported semiconductor chips [would be] coming soon.” Since then, however, there has been no further addition to the 10% baseline level for all goods entering the US.
The overall situation remains very fluid. One week after the initial reciprocal tariffs announcement came news of a 90-day pause on rates above 19% for 59 countries, with China being the most notable omission. Two days later, on April 12th, came an exemption for smartphones, computers and some other electronic devices from the 10% rate imposed elsewhere.
Fast forward to today, and a huge range of industries, including steel, automotive and pharmaceuticals, remain particularly vulnerable to existing and future tariffs, with escalating action likely to fragment global trade and limit the ability of companies to leverage international specialisation and expertise. This challenging trade environment also has the potential to stifle competition and innovation, with some industries in a position to benefit from protectionism while others face higher costs and reduced market access.
Unless policy positions soften, the technology industry remains vulnerable to any further changes in tariff rates. But how might this play out? Take the example of a company producing advanced memory chips with manufacturing facilities spread across the US, China and Taiwan. If a $100 chip made in Taiwan undergoes even a minor $5 packaging process in China, tariffs of up to 40% can inflate the final reimport cost to as much as $135 or $140. For businesses operating in sectors already characterised by tight margins, these additional costs cannot simply be passed on to customers without serious commercial risk. Instead, they add further pressure on already stretched supply chains.
No Quick Fix Solution
For European technology businesses reliant on semiconductor supply chains, the extreme volatility of the geopolitical landscape, compounded by the ongoing Ukraine war and escalating trade tensions, makes strategic planning extremely difficult.
That’s not to say there aren’t any options – the problem is, there is no ideal solution. While sourcing supplies from manufacturers in Mexico, Indonesia, Singapore and Malaysia is one potential route to avoid tariffs, it introduces new pressures around cost, capacity and the risk of future trade barriers should US policy change further.
Reshoring or nearshoring is no quick fix either. Although bringing production closer to home could help mitigate some risks, it assumes that suitable capacity is available at a competitive cost, which is not always the case. This leaves organisations across the continent in the invidious position of trying to balance rising costs, supply chain uncertainty and future-proofing strategies without any clear roadmap for what lies ahead.
Technology For Advanced Scenario Planning Is Key
Relying on traditional supply chain network and scenario reviews carried out once or twice a year is no longer enough. Instead, businesses need to be able to model different scenarios in real time to understand the potential impact of tariffs, cost changes and supply chain disruptions. This is where technology will play a crucial role. In particular, how organisations integrate advanced supply chain modelling tools, AI-driven scenario analysis, and digital twin technology into their existing processes will determine how effectively they can predict and respond to dynamic changes in circumstance.
In practical terms, this means deploying tools that can simulate multiple tariff scenarios, assess potential cost implications and then reconfigure supply chain networks as needed. By using digital twin technology, for instance, businesses can create a virtual model of their operations to test different strategies and identify the most resilient paths forward. Added to this, AI-driven scenario analysis and integrated business planning tools can further help organisations model the effects of tariffs on demand, sourcing, production and distribution.
With more advanced scenario modelling in place, businesses will also need to renew their focus on network design and optimisation to understand the impact of sourcing changes, production shifts and delivery routes. The effective use of real-time multi-enterprise visibility can strengthen this approach even further, allowing organisations to model supply chain risks and take corrective action before disruption takes hold.
With tariffs and trade restrictions threatening to impact everything from raw material availability to logistics costs, businesses need to be able to react quickly to fluctuations across the supply chain. Those that can adapt sourcing, production and distribution strategies in near real-time will be better positioned to absorb shocks and maintain competitiveness, especially as there remains so much scope for further volatility and unexpected change.
To explore how Blue Yonder’s advanced supply chain solutions can help your organisation navigate tariff uncertainty with real-time scenario planning, visit blueyonder.com.
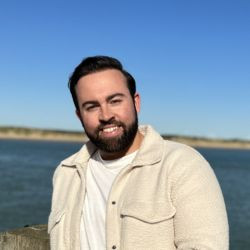