Mobile Manipulators: Wireless Inductive Charging System Enables New Era of Robotics
Technical Analysis | 10-05-2024 | By Jack Pollard
The following article, written by Marco van der Linden of PULS UK, explores Wiferion's innovative Wireless Power Kit, a ground-breaking advancement in industrial automation. Here are some key points from the article:
- Innovative Automation Solutions: Learn about Wiferion's Wireless Power Kit, a pivotal technology that combines autonomous mobile robots and collaborative robots. This section explores how inductive charging technology can drastically reduce downtime, enabling continuous operations and enhancing overall efficiency in industrial settings.
- Industry-Specific Applications: Discover how mobile manipulators equipped with Wiferion's technology are being implemented across diverse sectors such as logistics, healthcare, and semiconductor manufacturing. The article provides insights into how these innovations meet unique industry needs and drive automation forward.
- Case Study Insights: Gain a deeper understanding from a practical perspective as the article delves into how companies like OMRON are leveraging Wiferion's system to optimise their material handling tasks. This real-world application demonstrates the tangible benefits and increased productivity achieved through advanced robotic solutions.
Introduction
The growing shortage of skilled workers is increasing the pressure on industrial companies to automate their processes. Flexible, cost-effective and easy-to-implement robotics solutions such as autonomous mobile robots and collaborative robots are therefore in demand. Mobile manipulators connect both robot systems, but often cannot be used economically due to insufficient battery power. The solution: Wiferion's Wireless Power Kit, which enables inductive charging for both systems simultaneously.
Mobile Manipulators Can Do More Than Their Battery Power Allows
Collaborative robots (cobots) are one of the most dynamically growing segments of robotics. In contrast to conventional industrial robots, which have to be shielded from the human workplace by a protective device, they are designed for safe collaboration with humans. Mobile manipulators (MoMas) combine the advantages of cobots with those of autonomous mobile robots (AMR). A robot arm is mounted on an AMR. With MoMas, even more complex handling and transportation tasks can be automated with one system without having to install a stationary robot and a transport system with several AMRs. This makes this type of robot a flexible solution for a wide range of applications in industry, logistics and other areas. For the company, this means that investment requirements are reduced, as a separate robot is no longer needed for each process.
Mobile manipulators are ideal for:
- Pick-and-place applications
- Equipping and testing production machines and machine tools
- Material transportation
- Order picking of containers with assembled parts to the test station
- Vehicle inspection (e.g. cracks or paint on moving products)
- Laboratory automation
- Wafer production (semiconductor industry)
- Applications in the healthcare sector
The market for mobile manipulators has grown continuously in recent years. Experts assume that this trend will continue in the coming years. This is because, in most cases, complex automation solutions do not pay off for the automation of small parts handling for small and medium-sized series.
In practice, however, economical operation of the systems often fails due to the energy supply. As a MoMa combines two systems that were originally developed separately, the two technologies are often not considered as a holistic construct during design. The energy supply in particular proves to be a weak point. As the battery is only designed to supply the AMR, the operating time of the system drops rapidly if another power guzzler has to be supplied along with the robot arm.
This means that 24/7 operation of MoMas is hardly possible with the AMRs currently available on the market and their battery capacity. In order to bridge the downtimes, additional systems have to be purchased to take over during the charging breaks. This necessary oversizing of the MoMa fleet makes the cost-effectiveness of such systems considerably more difficult.
Wireless Power Kit Enables Complete System Consisting of AMR and Cobot
It is clear that the energy supply of MoMas must be thought through further if the systems are to reach the mass market. The problem is that there is hardly any space in the AMR platforms for additional batteries to extend the operating time. Integration into existing AMR models is difficult. One solution to this is the Wireless Power Kit, a system consisting of an intelligent charger and intelligent batteries. The kit is installed in the MoMa and efficiently supplies the complete system of AMR and cobot with sufficient energy for its tasks.
The Wireless Power Kit can be equipped with a scalable number of batteries and has an inductive charging system. It can be flexibly dimensioned depending on energy requirements. The energy system reliably supplies both a 24V and a 48V robot arm. In addition, it is possible to equip the kit with industry-standard DC/AC converters to provide any type of industrial power supply with 230 V AC (US 220/120V) or 400 V AC. This expands the possibilities of handling solutions that can be operated with the AMR if, for example, a robot arm only has an AC connection.
Inductive Charging Enables 24/7 Continuous Operation
In addition to a higher energy density, the Wireless Power Kit offers an inductive quick-charging system. This can increase the productivity of the MoMa by up to 32%. Wireless charging enables automated intermediate charging of the manipulator at pick or work stations. With in-process charging, the energy level of the vehicle battery remains constant. There is no need to fully discharge the battery and the associated long charging pauses.
The charging process takes place while the manipulators carry out their work. If a MoMa inserts new parts at a machine tool, for example, it is charged fully automatically and quickly for as long as the work step lasts. The process is repeated continuously at each subsequent work station. Even the shortest pauses of a few seconds can be used to supply energy. This makes 24/7 continuous operation of mobile manipulators possible for the first time.
Further advantages are:
- In contrast to conventional energy solutions with plug-in or sliding connections, the inductive battery charging system is a closed system without mechanical contacts. It works without component wear and therefore guarantees maintenance-free continuous operation.
- As no abrasion can occur on the charging contacts, MoMas can for the first time also perform handling tasks in critical clean room environments such as explosion-proof areas (EX), pharmaceuticals, laboratories or semiconductor production.
- Due to the high positioning tolerance, the factory navigation accuracy of all common AMRs is sufficient to ensure the positioning of the autonomous mobile robot at the charging point. Short circuits due to inaccurate positioning, which occur with contact chargers, are ruled out.
Already Successfully in Use: OMRON Relies on Wiferion
The Wiferion system offers an elegant solution that makes MoMas economical. Among others, OMRON, the preferred solution provider for companies that need to quickly find a way to automate material handling tasks performed by humans, relies on it. OMRON provides all the key components that make up a MoMa - the AMR, the cobot, the programmable logic controller (PLC) that controls both the AMR and the cobot, and the various sensors and user interfaces (HMIs) that are attached to the MoMa system depending on the application. Wiferion supplies the important additional component: the power supply. The Wiferion system enables the contactless charging that OMRON's customers in the semiconductor and cleanroom industries require and also provides the increased uptime needed in all production and storage facilities.
Conclusion
With the Wireless Power Kit, MoMas increase the quality and speed of processes and help companies to react quickly to changing market conditions. Employees can be relieved of undemanding and repetitive tasks and concentrate on value-adding tasks. Through inductive charging, Wiferion's battery solution enables 24/7 continuous operation and at the same time opens up the use of MoMas for additional activities and industries, such as the pharmaceutical industry and semiconductor production
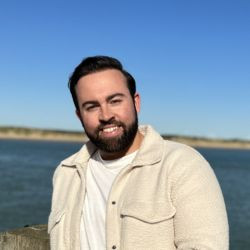