Electromagnetic Interference: A Growing Concern in Electronic Design
Articles | 09-09-2015 | By Mathias Goebel
Electromagnetic interference (EMI) is an increasing concern in modern electronic designs as the demand for higher operating frequencies and lower voltages continues to grow. In this article, Mathias Goebel, an experienced product manager at Avnet Abacus, sheds light on the challenges posed by EMI and offers valuable insights on how to mitigate its effects.
With a background in the electronics industry that spans over a decade, including working with TOKO, a Japanese manufacturer of Inductors, Transformers, and Filters, Mathias has gained a deep understanding of EMI and its implications in contemporary electronic systems. Join him as he explores the sources of EMI, the importance of proper grounding and shielding, and strategies for designing more resilient devices in today’s rapidly evolving technological landscape.
Modern designs are becoming more susceptible to EMI
EMI (electromagnetic interference) comes from unintended electromagnetic radiation caused by changing currents in other parts of the same or nearby circuits. This can affect signals, degrading, distorting or even destroying the signals present in transmission lines or radio signals.
EMI may be radiated or conducted and comes from most electrical or electromechanical devices, such as motors, power lines, antennas, and anything that carries an electrical signal, such as PCB traces (Ott, Henry W. Electromagnetic compatibility engineering. John Wiley & Sons, 2011.).
Although there are natural sources such as the sun, Northern Lights, and lightning, plus interference from nearby electronic systems and power lines, many sources of EMI are also found within the system itself. The power supply is often a culprit since it typically contains high-frequency switching components such as MOSFETs, which produce a lot of electrical noise.
The integrated circuits used in today’s high-tech electronic systems are evolving to use lower voltages and higher operating frequencies. This, unfortunately, makes them much more susceptible to EMI, which means the acceptable amount of noise in electronic systems is falling.
Example 1: Medical Devices In the healthcare industry, the increasing use of electronic medical devices, such as pacemakers, insulin pumps, and neurostimulators, has made EMI a critical concern. A well-documented case occurred in 2008 when a patient’s insulin pump malfunctioned due to EMI from a nearby mobile phone, causing an overdose of insulin and subsequent hypoglycemia (Electromagnetic interference from electronic devices used in the management of type 1 diabetes can impair the performance of an avalanche transceiver in search mode). This example highlights the importance of addressing EMI in electronic devices, especially in life-critical applications.
Example 2: Automotive industry EMI has become a significant issue due to the proliferation of electronic systems within modern vehicles. A notable case occurred in 2010 when Toyota recalled over 8 million vehicles worldwide due to unintended acceleration, partly attributed to potential EMI issues affecting the throttle control system (U.S. National Highway Traffic Safety Administration (2011). Technical Support to the National Highway Traffic Safety Administration on the Reported Toyota Motor Corporation Unintended Acceleration Investigation). This incident underscores the need for rigorous EMI testing and mitigation strategies in the design of automotive electronics to ensure safety and reliability on the road.
EMI should be considered from the start
EMI can do more than just distort signals – in extreme cases. It can cause complete system failure. Manufacturers are responsible for ensuring that electronic devices are not susceptible to EMI but also to ensure their devices are not producing noise that could interfere with other systems’ EMC (electromagnetic compatibility), as outlined in Federal Communications Commission (FCC) guidelines. Considering EMI from the beginning of the design process is crucial, as addressing unforeseen EMI problems later on, can be extremely time-consuming and expensive, especially if a design has been completed and failed testing. Infineon provides useful EMI/EMC and System-ESD Design Guidelines in their application report (EMC and System-ESD Design Guidelines for Board Layouts).
An initial system assessment should reveal which parts of the design are potential noise sources and which are particularly sensitive to EMI. Potential noise sources, including power supplies, should be located as far as possible from any sensitive ICs. It’s important to consider this before design options become limited further down the line.
Grounding is not trivial
Potential sources of EMI should be identified early on and blocked, and low-impedance paths to ground should be provided for any EMI currents. They should be as short as possible since even a few centimetres can make a significant difference for signals more than a few kilohertz.
On PCBs, ground planes are used. Any EMI susceptible tracks must be run above the ground plane, avoiding any areas where there are breaks in the ground plane. Traces placed too close to the edge of the ground plane can also cause problems due to fringing effects.
If grounding is neglected and loops are allowed to form, voltages can be induced due to magnetic coupling, and/or signals can be radiated, both of which cause EMI issues. Grounding is not trivial. Potential sources of EMI should be identified early on and blocked, and low-impedance paths to ground should be provided for any EMI currents. NASA’s Technical Paper on Electromagnetic Compatibility Design Guide offers more detailed guidance and best practices for grounding in avionics and related ground support equipment (NASA (1980). Electromagnetic Compatibility Design Guide for Avionics and Related Ground Support Equipment).
Board-level shielding also depends on proper ground design
If, even with proper grounding and layout, EMI is still a problem, then shielding can be used to reduce or eliminate radiated noise from parts of the system. A typical implementation might be a metal can or grate placed over the offending component or subsystem. Again, because the ground plane of the PCB is effectively one side of the can, ground plane design can affect how well the shield works. Any vias (vertical interconnect accesses) or traces entering the shielded area are potential areas where noise could escape.
Other factors affecting how well shields work include near-field effects (which occur when the shield is too close to the source) and resonances (at high frequencies, resonances can induce strong oscillations, adding to the EMI problem).
Screened enclosures are effective but expensive (and often ugly)
System-level shielding is implemented via screened enclosures, typically conductive boxes that are connected to the ground, which can be an effective way to prevent radiated noise from penetrating or escaping the system. However, this option can be expensive. High-quality screened enclosures will have as few joints/seams as possible, as these are weak points where EMI can be radiated. EMI filters can be added to any cables or interfaces to the enclosure, and the cables themselves can be screened too.
Non-conductive enclosures with a conductive coating can also be used; they can be more aesthetically pleasing than the ‘big metal box’, which represents most screened enclosures, though they are not usually as effective.
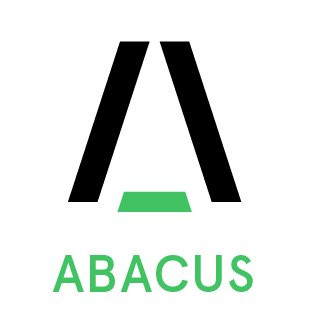