The Challenges of Inline Thickness Measurement
27-03-2024 | By Jack Pollard
Maintaining correct material thickness is critical in precision manufacturing. Micro-Epsilon addresses this challenge, presenting the complexities and solutions for inline thickness measurement. Explore how their advanced sensors and systems can enhance accuracy and efficiency in production processes.
When selecting an in-process system for measuring the thickness of film, plate or sheet materials, a number of challenges need to be considered, including sensor alignment, linearity and the effects of thermal changes, says Glenn Wedgbrow, Business Development Manager at Micro-Epsilon UK.
There are many reasons why we need to measure thickness. All materials have a tolerance in production, so any materials that are too thin or too thick could cause a problem further down the line or at the end customer’s site. Changes in thickness during production can indicate wear of components, for example, in extrusion dies or on rolling stands. Monitoring trends can point to early warning signs.
The traditional method of checking thickness is often to take a measurement sample from the start of the production run and then again at the end. But what happened in the middle? If you find the material is out of tolerance, that’s a lot of scrap to consider. So you might choose to take more readings during the process. If these checks are being done manually, they often require the production line to stop. Most process variability will come in ‘start’ and ‘stop’ phases, so keeping a line running is generally key to improving consistency. Ultimately, checking the product thickness as it’s produced ensures that the end customer receives the quality of product expected.
Target material types and the production processes used all have a bearing on how the thickness of a product can be measured. Sometimes it is based on the setting of a gap on a roller or adjustment of dies in an extrusion head. It could be liquid poured and cured such as glass, rubber or metal. It could also be part of a secondary process where the basic material is already produced, but is then combined with similar or differing materials as multiple layers, or even woven strands that are then bonded such as carbon fibre.
Let’s now consider some of the challenges of measuring thickness.
Single-Sided Measurements
Perhaps the simplest thickness measurement is a single-sided measurement against a reference or datum surface. First, the sensor is zero’d on the datum surface and the target to be measured is inserted. The reading of the sensor is changed or displaced by the material thickness. There are a number of uncertainties with this method. If the reference or datum moves after mastering, the reading will be incorrect. Similarly, if the target does not sit correctly on the datum surface, the air gap will also be included in the measurement. The same issue can also occur with tilted targets.
If we are only allowed to view a target from one side, we must consider if we can combine technologies to enable accurate measurements. Where we have a mix of different material types, we can utilise those different material properties to our advantage. For example, an eddy current sensor in combination with a laser triangulation sensor can be used to measure sprayed skin thickness. The eddy current sensor measures the distance to the nickel-coated spray mould and has an opening in the centre through which the laser sensor measures the distance to the sprayed part. Eddy current sensors only measure against metallic targets and therefore see straight through the non-metallic sprayed coating. The use of an air coil in eddy current sensors from Micro-Epsilon makes this combination possible, as the laser sensor can look through the eddy current sensor at the same measuring point. When both signals are subtracted, the thickness of the applied sprayed skin is measured.
Another well used sensor combination is achieved with eddy current and capacitive sensors for non-metallic materials passing over a roller. Movement of the metal roller is considered by the eddy current sensor and the capacitive sensor measures the material or coating thickness.
Single-Sided Measurements – Special Case
If the target is transparent, it is possible to make an absolute measurement of the material thickness from one side using only one sensor with Interferometer or confocal technology.
The use of light refraction creates ‘edges’ or return signals that indicate the transition between the air and the material. Knowing the refractive index of a material enables the accurate measurement of the material thickness provided it stays within the measurement or working range of the sensor.
Measuring from Both Sides
If single-sided measurement is not suitable or the challenges cannot be overcome, in many cases customers want to know the true material thickness by measuring the material in ‘free space’, which requires having space on both sides of the material so that a measurement can be taken from both surfaces.
When you consider this set up, there are a number of challenges that must be considered and either overcome or accepted.
Sensor Alignment
The sensors must be positioned so that the measuring spots coincide ‘through’ the full measurement range of the sensor. There should be no offset, tilt or inclination of the sensors in relation to the measurement object. For example, with a sensor offset of 1 mm and inclination of 2°, the effective error equals 35 µm, and at 10 mm target thickness increases to 41 µm.
Particularly with laser triangulation sensors, the location of the beam spot to the sensor housing should be noted. It should not be assumed that two apparently identical sensors will position the spot in the same place. Standard sensor housings are not usually precise enough for precision thickness measurements unless time is taken to align them correctly. To help customers make their own thickness set ups, the ILD1900 sensor from Micro-Epsilon uses an innovative sleeve mounting arrangement to tighten the spot spacing from housing to housing.
When you have two sensors looking at the same target, you must consider that each sensor has its own cycle time. If your target is vibrating or moving in the gap between the sensors then it’s very easy to introduce an error. Consider a target oscillating up and down by 1mm at 20Hz (times a second). A difference in capture time of 1ms between your sensors would equate to an error of 125µm.
Positioning of the Sensors/Measuring Range
The next challenge is the relative position of the sensors and their measurement ranges.
Depending on how the sensors are arranged, the position of the target edges must stay within the measuring field. If the sensors are set so that the measuring zones do not overlap, then situations can arise where one sensor may not see the target. Consideration should also be given to process ‘start’ and ‘stop’ conditions, for example, is the material held in tension at all times? Speed changes in the line can induce upward or downward movement. Is the setup able to capture these events if needed? Ideally, the sensor ranges should overlap and cover the full range of material movement or at least control the movement.
Linearity
The accuracy of a sensor is often referred to as its linearity. The linearity value describes the deviation from the ideal, straight characteristic curve. Each measurement sensor has its own measurement uncertainty, or non-linearity. This means that at any given point in the measuring range the actual reading from a sensor can vary by a percentage of its measuring range. So taking just two sensors without any additional processing means that both sensors’ uncertainties need to be considered with respect to the accuracy looking to be achieved. For example, without adjustment, just moving a target 200 micron up or down can result in errors of 8 micron. The position in the range also has potential to affect the true value. To solve this, the sensors must be calibrated together as a whole.
Effects of Thermal Changes
Even when the sensors have been aligned and synchronised, there is still a further challenge that can affect everything – thermal changes. When measuring a target thickness in free space, the gap between the sensor and the opposite sensor is critical, as this is the constant on which the differential measurement is based. Taking a mechanical frame with a pair of sensors and cycling the temperature shows that the effective change with just a 5°C swing is up to 20 micron.
System Capability
The final challenge – if the previous ones have been overcome or the errors associated have been accepted – is to prove the capability. Exactly how do you check or confirm the performance of your solution? There are two factors to consider here: the system repeatability, i.e. how much variability in the measurement system is caused by the measurement device, and reproducibility – how much variability is caused by different operators.
For more information, please visit www.micro-epsilon.co.uk or call the Micro-Epsilon sales department on +44 (0)151 355 6070 or email info@micro-epsilon.co.uk.
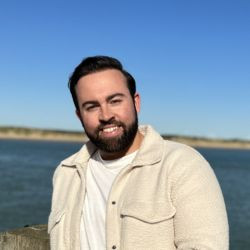